A brand new analysis challenge exhibits how 3D printing and machining can lastly work in sync. Led by researchers on the Vienna College of Know-how in Austria (TU Wien), the challenge goals to plan and optimize each step of hybrid manufacturing, from 3D printing to machining, earlier than manufacturing even begins.
A group of engineers from TU Wien’s Institute of Manufacturing Engineering and Photonic Applied sciences (IFT) developed smarter methods to mix additive and subtractive manufacturing (or machining) processes in a single, streamlined workflow. If achieved proper, this hybrid manufacturing can save time, reduce prices, and cut back waste, particularly in factories that make giant or advanced components.
3D printing and machining, which are sometimes handled like two separate worlds, will be introduced collectively in a method that’s really sensible for producers.
From Metallic Wire to Completed Half
The analysis targeted closely on Wire Arc Additive Manufacturing (WAAM), a way used to 3D print giant metallic components utilizing welding wire. WAAM is right for creating large, heavy-duty parts, however these components nonetheless have to be milled or smoothed out afterward. That’s the place issues typically get difficult and costly, the consultants clarify.
Based on the group, they discovered methods to foretell how every 3D printed half would behave earlier than printing even begins. Utilizing digital simulations, they might estimate how the half would shrink, the place it would warp, and the way a lot materials would have to be eliminated.
In addition they examined machine hammer peening, a way that smooths and strengthens the floor of a printed half earlier than it’s machined. They mixed it with different remedies like shot peening, which makes use of small metallic balls to toughen the floor, and Hirtisation, a chemical course of that removes tough edges and leftover powder. The mix led to extra uniform and sturdy components.
IFT’s large contribution was a simulation mannequin that helps factories plan printing and machining prematurely. This consists of calculating how a lot further materials must be printed to permit for ending, the place stresses or tough spots would possibly seem, and how one can machine the half extra effectively afterward. The result’s much less materials waste, shorter machining time, and fewer surprises.
Making It Work for Small Producers
Whereas hybrid manufacturing sounds high-tech, the challenge was designed with small and medium-sized firms (SMEs) in thoughts. Many of those companies are fascinated with 3D printing however don’t have the assets for sophisticated workflows or costly high quality management setups.
The IFT group labored straight with 15 Austrian firms to check and validate real-world purposes, ensuring the instruments they developed might really be utilized in day-to-day manufacturing facility settings, together with approaches for the seamless integration of WAAM processes into present manufacturing traces. The aim was all the time to make hybrid manufacturing extra inexpensive, scalable, and sensible.
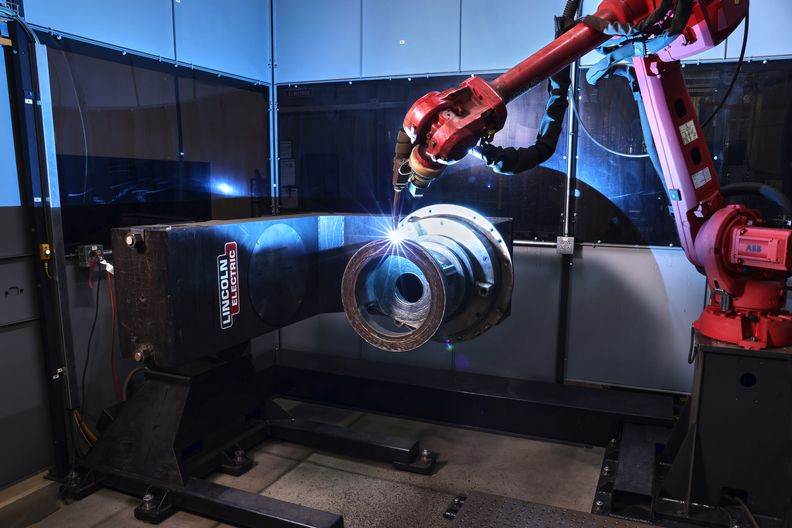
A robotic welder builds a chunk of apparatus layer by layer utilizing its wire-arc additive manufacturing course of. Picture courtesy of Lincoln Electrical.
One other a part of the challenge targeted on creating a wise software program system that may regulate how machines transfer primarily based on real-time sensor information. This technique, described as a CAM rule engine, is linked to a central database that collects info from each step of the manufacturing course of. Collectively, they assist factories transfer nearer to completely automated, data-driven manufacturing.
A Workforce Effort Throughout Europe
This work was half of a bigger worldwide effort known as Superior Processing of Additively Manufactured Components – Part II (Advert-Proc-Add II), a analysis challenge targeted on enhancing how 3D printing and machining work collectively in actual manufacturing facility settings. The challenge introduced collectively groups from Austria, Germany, and Belgium, together with universities, trade teams, and analysis institutes. Companions just like the Institute for Machine Instruments on the College of Stuttgart, the Institute for Machining Know-how at TU Dortmund, and KU Leuven in Belgium all contributed to creating hybrid manufacturing sooner, smarter, and simpler to undertake.
What’s extra, trade teams just like the ecoplus Mechatronics Cluster and Analysis Affiliation for Mechanical Engineering (FKM) in Germany helped flip the analysis into actual instruments that firms can really use of their factories.
It was funded by nationwide innovation companies from every nation, with robust backing from Austria’s Analysis Promotion Company and Germany’s Ministry for Financial Affairs and Local weather Motion.
This challenge proves that 3D printing and machining can work collectively in a better, extra sensible method, in order that 3D printing isn’t remoted from the remainder of the manufacturing facility ground. Ultimately, it should assist join additive and subtractive processes, making them usable for on a regular basis producers.
The findings might be offered on the World Machine Device Exhibition (EMO) 2025 in Hanover, one of many world’s greatest commerce festivals for industrial manufacturing.
Subscribe to Our Electronic mail E-newsletter
Keep up-to-date on all the most recent information from the 3D printing trade and obtain info and presents from third get together distributors.