Velo3D, a U.S.-based steel 3D printer producer, has introduced it’s advancing its materials qualification course of for C103 Niobium and Ti-6Al-4V Titanium powders manufactured by Amaero Ltd, a producer of high-value specialty alloy powders. This determination follows the profitable completion of a key testing milestone carried out by Auburn College’s Nationwide Middle for Additive Manufacturing Excellence (NCAME).
The initiative underscores the businesses’ broader dedication to establishing a strong U.S.-based additive manufacturing provide chain for high-stakes aerospace and protection purposes. “To attain the total potential of steel additive manufacturing, it’s important to construct a resilient home ecosystem—from scalable powder manufacturing to machine platforms and high-performance components. Amaero has commissioned essentially the most superior atomization expertise for refractory and titanium alloys and is proud to help the U.S. industrial base. This milestone with Auburn and our broader partnership with Velo3D are vital steps towards scaling reasonably priced, high-quality, traceable powders for nationwide safety purposes,” stated Amaero Chairman and CEO Hank J. Holland.


Strategic Collaboration Helps U.S. Aerospace and Protection
As a part of the strategic partnership between Velo3D and Amaero, NCAME printed and evaluated the powders to confirm they meet AM requirements. The outcomes fulfilled Velo3D’s preliminary standards for initiating system-specific testing on its Sapphire printer line. Extra particularly, Amaero’s C103 powder handed ASTM F3635 Class B necessities after present process a 2200°F warmth therapy. As well as, Amaero’s Ti-6Al-4V powder met AMS7015 and ASTM F3001 requirements.
With this preliminary qualification now full, Velo3D will start in-house validation and print testing utilizing its Sapphire methods to totally combine the supplies into its manufacturing workflows.
“Velo3D lauds the current milestone achievement between Amaero Ltd and NCAME,” stated Dr. Arun Jeldi, CEO of Velo3D. “The shut collaboration between Amaero and NCAME has demonstrated Amaero’s powder conformance with additive manufacturing business requirements. On account of Amaero’s accelerated achievement, we’re excited to announce that below the Velo3D/Amaero strategic partnership, over 1,000 kg of Niobium and Titanium powder will arrive on the Velo3D manufacturing ground late in Q3CY2025 to help vital tasks within the aerospace and protection industries.”
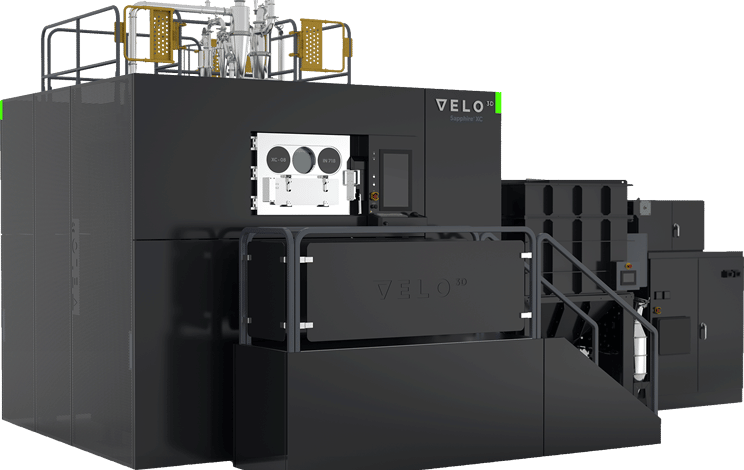
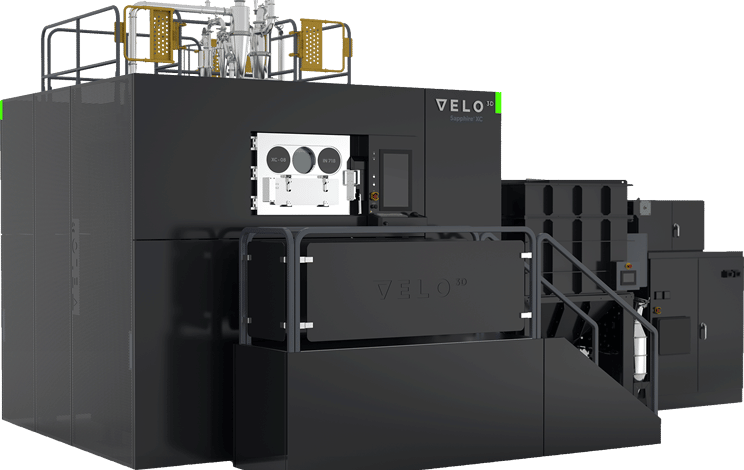
Materials Qualification and Strategic Partnerships
Throughout the AM sector, firms are more and more investing in strategic partnerships and materials qualification processes to make sure reliability, traceability, and scalability.
In March, PyroGenesis, a Canadian steel powder producer, formally confirmed Boeing because the aerospace OEM in its Ti64 steel powder qualification course of, ending months of hypothesis. The corporate’s Ti64 “coarse” steel powder efficiently met Boeing’s technical requirements, positioning PyroGenesis within the last levels of the approval course of.
In February, Eire-based Croom Medical and US-based tantalum merchandise provider World Superior Metals (GAM) developed a closed-loop provide chain method to increase the usage of tantalum in 3D printing. By tackling the fabric’s processing challenges and making its use extra sustainable, the 2 firms are making certain a gentle, recyclable provide of tantalum powder for medical purposes. Their course of depends on Colibrium Additive’s M2 laser powder mattress fusion (LPBF) expertise to enhance printing effectivity, making tantalum a extra sensible possibility for 3D printed implants.
What 3D printing tendencies do you have to be careful for in 2025?
How is the way forward for 3D printing shaping up?
To remain updated with the newest 3D printing information, don’t neglect to subscribe to the 3D Printing Trade publication or comply with us on Twitter, or like our web page on Fb.
When you’re right here, why not subscribe to our Youtube channel? That includes dialogue, debriefs, video shorts, and webinar replays.
Featured picture reveals Refractory Powders. Picture through Amaero.