Researchers at The College of Texas at Dallas have created a 3D-printed foam that provides improved sturdiness and recyclability in comparison with standard polymer foams. The brand new materials, detailed within the March 1 print version of RSC Utilized Polymers, was developed by means of a two-year analysis mission led by doctoral scholar Rebecca Johnson. The staff efficiently demonstrated their idea by producing foam within the form of a balloon canine, showcasing the flexibility to create advanced, personalized shapes.
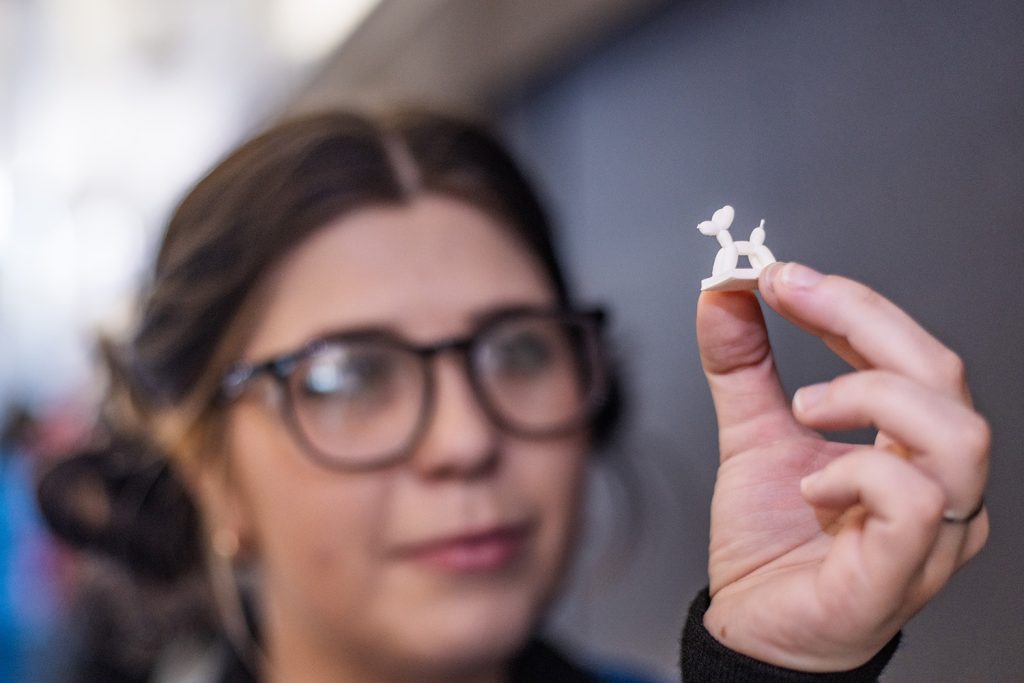
“The objective of the mission was to handle some limitations in 3D printing when it comes to making polymer foam,” stated Dr. Ron Smaldone, affiliate professor of chemistry and biochemistry and the examine’s corresponding creator. “One of many principal makes use of, or pursuits, for 3D-printable foams is insulation and shock absorption.”
In contrast to conventional thermoset foams that can’t be reshaped or recycled as soon as molded, the UT Dallas foam makes use of dynamic covalent chemistry with reversible bonds. This method permits the fabric to restore itself when broken, probably extending its usable life. In accordance with Smaldone, with additional analysis, any such foam may very well be utilized in high-impact absorption functions reminiscent of helmets, automobile bumpers, or armor.
The researchers confronted vital challenges in making the polymer formulation suitable with 3D printing expertise. Nonetheless, this manufacturing technique permits the creation of extra advanced constructions like positive lattices, which might improve the fabric’s bodily flexibility and utility versatility.
Chemistry doctoral scholar Ariel Tolfree, who co-led the examine with Johnson, plans to increase the analysis by analyzing methods to reinforce the froth’s recyclability and sustainability potential. The mission obtained funding from The Welch Basis, the Nationwide Science Basis, and the Division of Vitality.
Supply: information.utdallas.edu