Penn State researchers have developed a brand new multi-material 3D printing approach that efficiently fuses two completely different metals right into a single complicated construction. The crew used a course of known as multi-material laser powder mattress fusion to print a construction combining low-carbon chrome steel and bronze. This achievement was made doable by Penn State’s Heart for Modern Supplies Processing By means of Direct Digital Deposition (CIMP-3D), which acquired an Aerosint selective powder deposition system in August 2023.
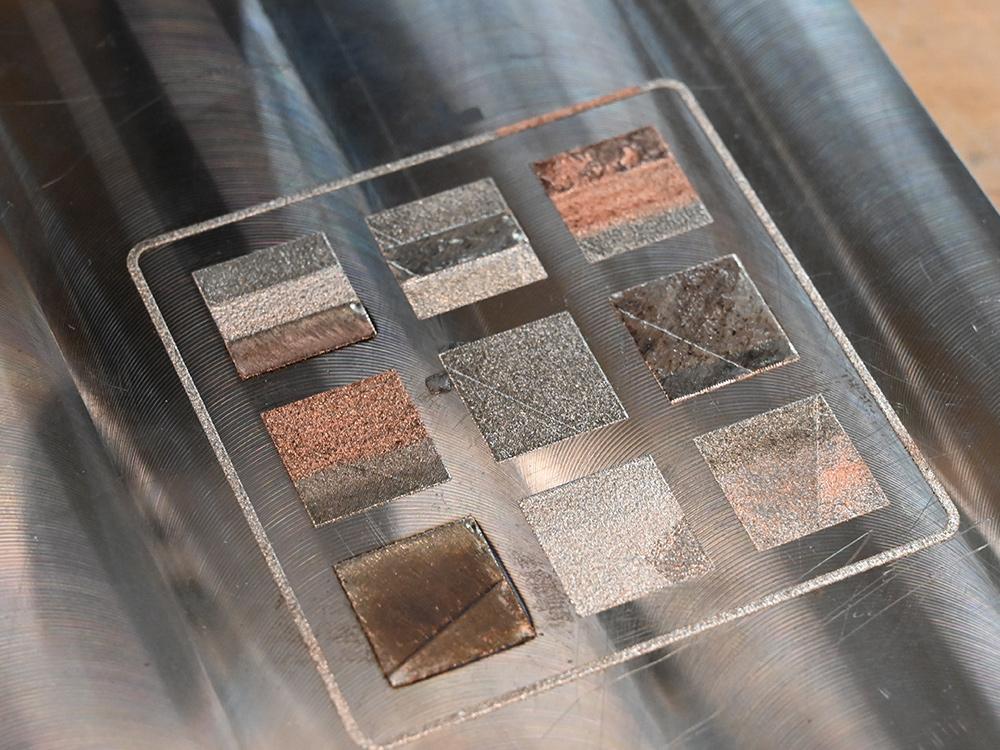
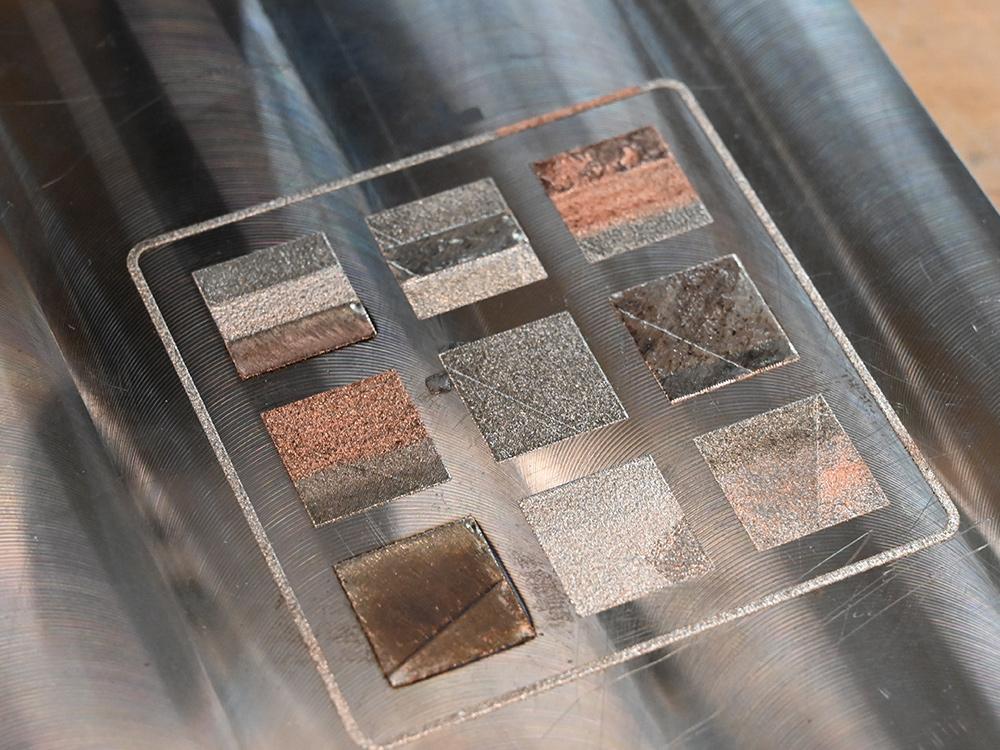
“In a course of known as selective powder deposition, we are able to now soften a number of powdered metals in a single layer through the additive manufacturing course of — and we have been the primary college within the U.S. to take action,” mentioned Jacklyn Griffis, doctoral candidate in mechanical engineering and first creator of the paper printed in npj Superior Manufacturing.
The researchers centered on analyzing how construct orientation affected the standard of the ultimate product. They created a fancy form referred to as a gyroid, which has functions in warmth exchangers and biomedical implants. The crew examined defects reminiscent of cracking and porosity, interfacial microstructures, and factor diffusion throughout the interface to know how these elements impacted efficiency.
“Penn State has all the time been a pacesetter in steel additive manufacturing, however we now have the flexibility to fabricate complicated multi-material elements, the place we can’t solely make complicated designs however management exactly the place every materials is positioned,” defined Guha Manogharan, affiliate professor of mechanical engineering and co-director of CIMP-3D.
The analysis crew makes use of CT scans to supply digital 3D renderings of elements, permitting them to establish potential points like pores and micron-scale defects. This functionality permits real-time monitoring of the manufacturing course of. In response to Griffis, a one-centimeter-tall steel half consists of 1000’s of layers of steel powder and takes a number of hours to print.
Future work will give attention to remodeling this 3D printing technique right into a extra strong, production-ready course of by in-process monitoring. The crew additionally plans to include further steel alloys reminiscent of Inconel and copper. The analysis was supported by the Utilized Analysis Laboratory’s Walker Graduate Assistantship and the U.S. Nationwide Science Basis.
Supply: psu.edu