James Bruton, a UK-based engineer and YouTuber, has accomplished an omnidirectional bike utilizing 3D printed elements, aluminum extrusion, and a self-balancing management system. The design options two omni wheels mounted at 90 levels to 1 one other, enabling the car to journey in any course, together with straight sideways. Bruton reused the entrance wheel from a one-wheel balancing robotic inbuilt April 2025 and the rear wheel from his earlier 2023 speeder bike venture.
Aluminum 4040 T-slot extrusion varieties the chassis, linked with sloped and right-angle brackets to carry the reused robotic fork meeting in entrance and a belt-driven motor help in again. Axle holders and drivetrain pulleys have been fabricated utilizing LulzBot 3D printers, together with the TAZ Workhorse and Mini 3. Bruton printed giant structural elements with 1.2 mm nozzles for sooner construct occasions. Polymaker’s PolyMax PLA was used for structural elements, whereas PolyLite Professional filament supported the electronics enclosure. Rear wheel hubs have been created from plywood resulting from measurement limitations on the printer mattress.


The drivetrain features a two-stage belt discount system. The primary stage delivers a 3:1 torque improve utilizing an intermediate pulley, adopted by an HTD8-profile belt connecting to a big ultimate pulley on the rear wheel. The rear drive system is powered by a single ODrive S1 servo motor equipment. ODrive, an organization specializing in open-source motor controllers, provides the brushless motor and encoder meeting able to delivering as much as 2 kW. The system’s rigidity could be adjusted by sliding the motor mount alongside the extrusion body, securing it with braced aluminum plates.
A PID controller maintains steadiness utilizing knowledge from a BNO086 inertial measurement unit. A Teensy 4 microcontroller processes roll knowledge and regulates wheel torque accordingly. The management panel homes an emergency cease, begin button, voltage displays, trim adjustment, and a spirit degree for orientation reference. A 500-amp contactor isolates motor energy. Two pairs of 6S lithium polymer batteries in collection provide 50V to the motor drivers and 12V to auxiliary methods.
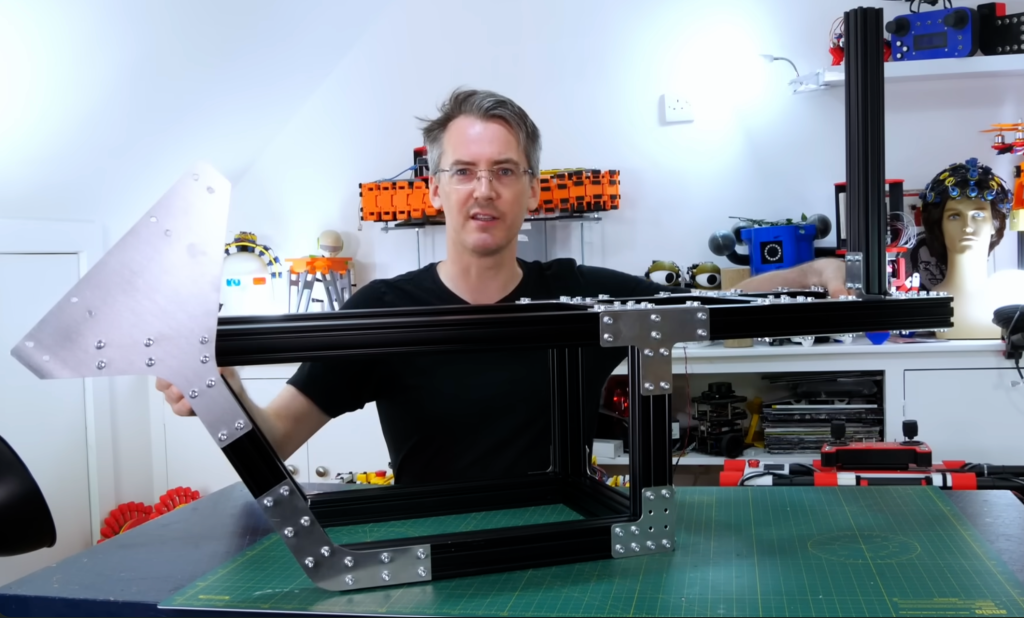
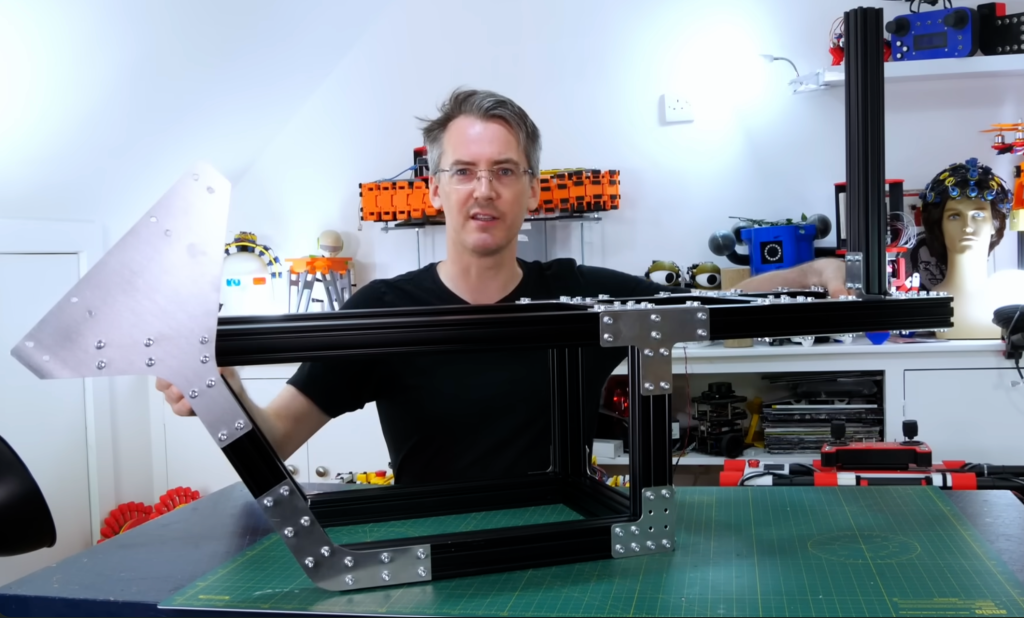
Bruton changed earlier twist-grip enter methods with two three-axis joysticks. The proper-hand joystick handles ahead, backward, and lateral motion. The left-hand stick controls rotation. Analog alerts are processed via a smoothing filter adjustable through a management knob, permitting gradual deceleration when the joystick is launched. Bruton noticed that the filter improves experience high quality by softening sudden adjustments in enter.
Joystick enter alters the PID controller’s setpoint, which defaults to 0°, representing upright steadiness. Changes to this setpoint permit the bike to lean and transfer concurrently, much like how a rider leans into turns. Bruton fine-tuned the PID parameters via trial and error, rising the integral time period to make sure that extended lean angles result in elevated motor response. He used minimal by-product correction to cut back overshooting and oscillations.


Preliminary testing confirmed that the rear omni wheel alone may stabilize the body. When each wheels have been lively, the bike achieved omnidirectional motion. Nonetheless, steering uncovered torque imbalances. The rear wheel generated considerably extra rotational pressure than the smaller entrance unit. When Bruton tried to rotate in place, the chassis tipped beneath load, inflicting the entrance wheel to overcorrect and destabilize the body. To compensate, he leaned reverse the meant flip course, counteracting the chassis torque.
To simplify management, Bruton reconfigured the bike for reverse using. He mounted the joystick interface on the rear and reversed stick mappings. Along with his weight now positioned over the bigger rear wheel, torque disturbances diminished and steering response improved. “Now I can flip simply positive… simply lean the best way I wish to go and off we go,” he famous after reorienting the controls.
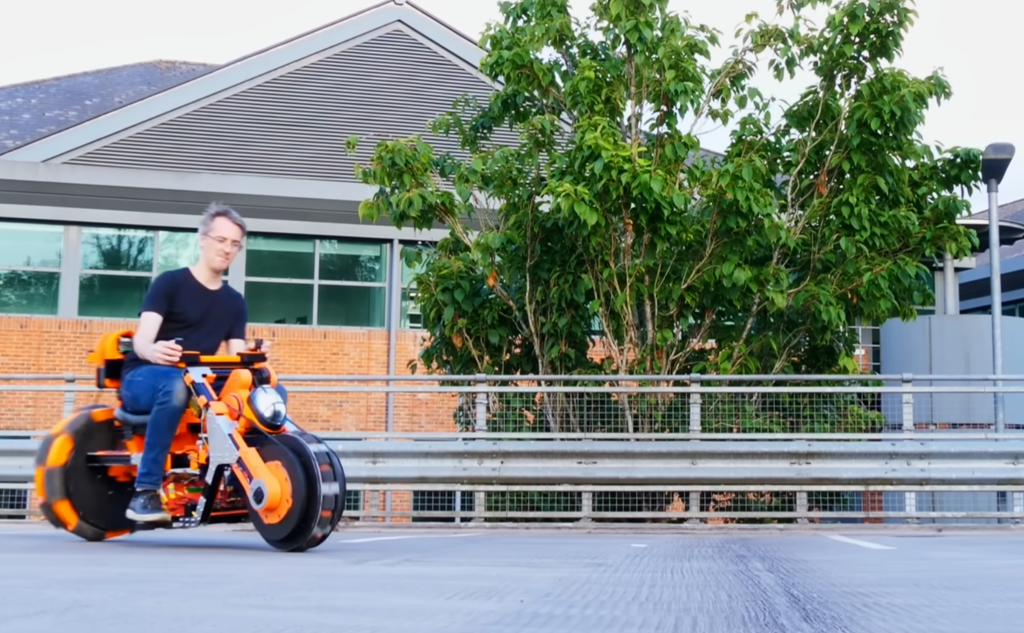
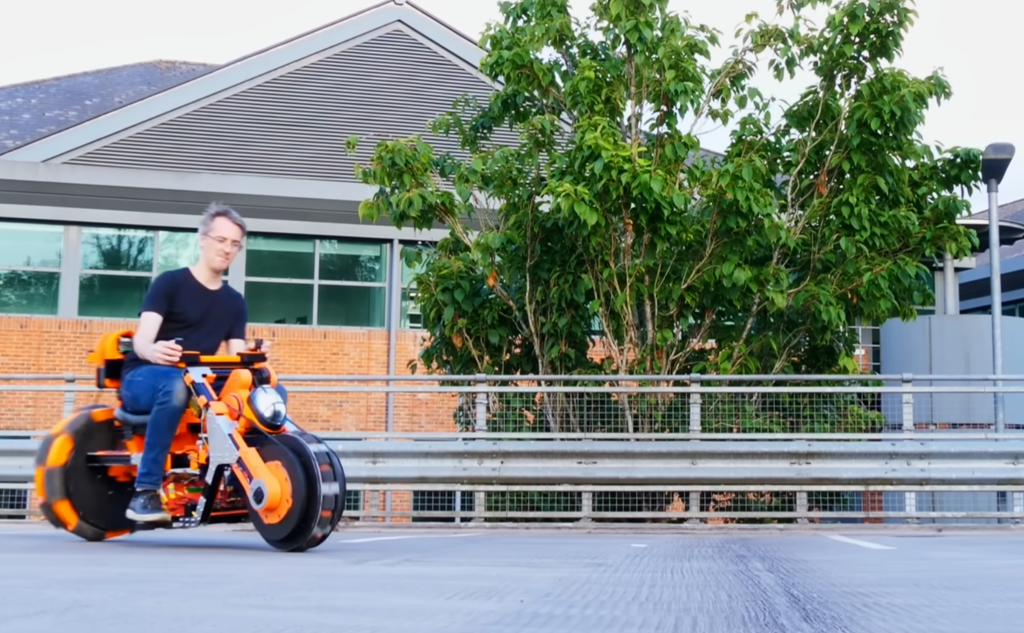
Regardless of mechanical success, the system has limitations. The small rollers on the entrance wheel require excessive present—round 20 amps at 50 volts even with out load—which limits effectivity. The rear motor gives extra torque than the entrance can compensate for, limiting balanced rotation at greater speeds. Bruton discovered that using backward produced higher management, as his middle of mass aligned with the extra highly effective wheel.
All venture recordsdata, together with CAD designs and management firmware, can be found on GitHub: https://github.com/XRobots/TwoOmniWheelBike.
Prepared to find who gained the 2024 3D Printing Trade Awards?
Subscribe to the 3D Printing Trade publication to remain up to date with the newest information and insights.
Featured picture exhibits CAD mannequin of the omnidirectional bike. Picture through James Bruton.