Researchers on the Nationwide Institute of Requirements and Know-how (NIST) have recognized quasicrystals in a 3D-printable aluminum alloy, in accordance with a research revealed within the Journal of Alloys and Compounds. NIST supplies engineer Andrew Iams found the distinctive atomic association whereas analyzing the alloy with an electron microscope. The findings assist clarify why sure aluminum-zirconium alloys might be efficiently 3D printed with out cracking points that usually have an effect on high-strength aluminum supplies.
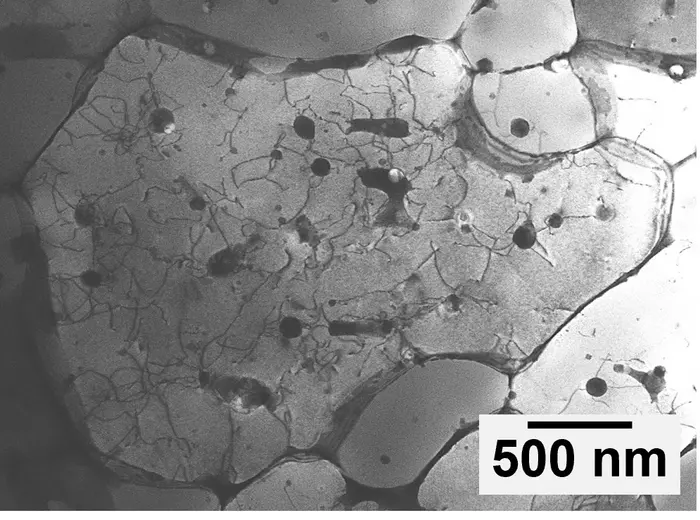
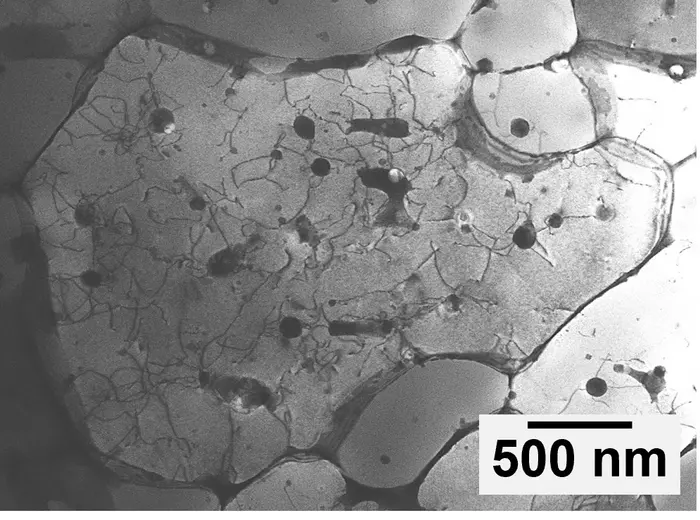
Steel 3D printing, significantly powder mattress fusion, melts metallic powder layer by layer utilizing high-powered lasers. The method creates geometries unattainable to realize by way of conventional manufacturing strategies. Nevertheless, most high-strength aluminum alloys crack throughout printing, limiting their use in additive manufacturing functions.
The analysis staff found that quasicrystals – buildings with uncommon symmetry patterns – type within the aluminum-zirconium alloy through the excessive heating situations of the printing course of. Utilizing superior imaging methods, Iams confirmed the presence of quasicrystals by observing their distinctive fivefold, threefold, and twofold symmetry from varied angles. These buildings disrupt the metallic’s uniform crystalline sample, creating defects that improve the alloy’s power.
The research addresses a major problem in 3D printing aluminum. Whereas conventional aluminum melts at roughly 700 levels Celsius, metallic 3D printing entails temperatures exceeding 2,470 levels Celsius, which considerably alters materials properties. Researchers discovered that including zirconium helps stabilize the aluminum throughout these excessive situations.
This analysis might result in new approaches in designing metallic alloys particularly for additive manufacturing. By understanding how quasicrystals contribute to materials power, engineers may probably develop aluminum alloys with improved properties for aerospace parts, warmth exchangers, and automotive elements. The research’s outcomes have specific significance for industries requiring light-weight but sturdy supplies that may be produced by way of 3D printing.
Supply: scienmag.com