Instructing a robotic new expertise used to require coding experience. However a brand new era of robots might doubtlessly be taught from nearly anybody.
Engineers are designing robotic helpers that may “be taught from demonstration.” This extra pure coaching technique permits an individual to steer a robotic by a activity, usually in one in all 3 ways: by way of distant management, comparable to working a joystick to remotely maneuver a robotic; by bodily shifting the robotic by the motions; or by performing the duty themselves whereas the robotic watches and mimics.
Studying-by-doing robots normally prepare in simply one in all these three demonstration approaches. However engineers on the Massachusetts Institute of Expertise (MIT) have now developed a three-in-one coaching interface that enables a robotic to be taught a activity by any of the three coaching strategies. The interface is within the type of a handheld, sensor-equipped device that may connect to many frequent collaborative robotic arms. An individual can use the attachment to show a robotic to hold out a activity by remotely controlling the robotic, bodily manipulating it, or demonstrating the duty themselves — whichever type they like or most closely fits the duty at hand.
The MIT group examined the brand new device, which they name a “versatile demonstration interface,” on a regular collaborative robotic arm. Volunteers with manufacturing experience used the interface to carry out two handbook duties which are generally carried out on manufacturing unit flooring.
The researchers say the brand new interface presents elevated coaching flexibility that might broaden the kind of customers and “lecturers” who work together with robots. It might additionally allow robots to be taught a wider set of expertise. As an example, an individual might remotely prepare a robotic to deal with poisonous substances, whereas additional down the manufacturing line one other individual might bodily transfer the robotic by the motions of boxing up a product, and on the finish of the road, another person might use the attachment to attract an organization emblem because the robotic watches and learns to do the identical.
“We try to create very smart and expert teammates that may successfully work with people to get advanced work performed,” stated Mike Hagenow, a postdoc at MIT within the Division of Aeronautics and Astronautics. “We consider versatile demonstration instruments can assist far past the manufacturing ground, in different domains the place we hope to see elevated robotic adoption, comparable to residence or caregiving settings.”
Hagenow will current a paper detailing the brand new interface, on the IEEE Clever Robots and Programs (IROS) convention in October. The paper’s MIT co-authors are Dimosthenis Kontogiorgos, a postdoc on the MIT Pc Science and Synthetic Intelligence Lab (CSAIL); Yanwei Wang PhD ’25, who not too long ago earned a doctorate in electrical engineering and pc science; and Julie Shah, MIT professor and head of the Division of Aeronautics and Astronautics.
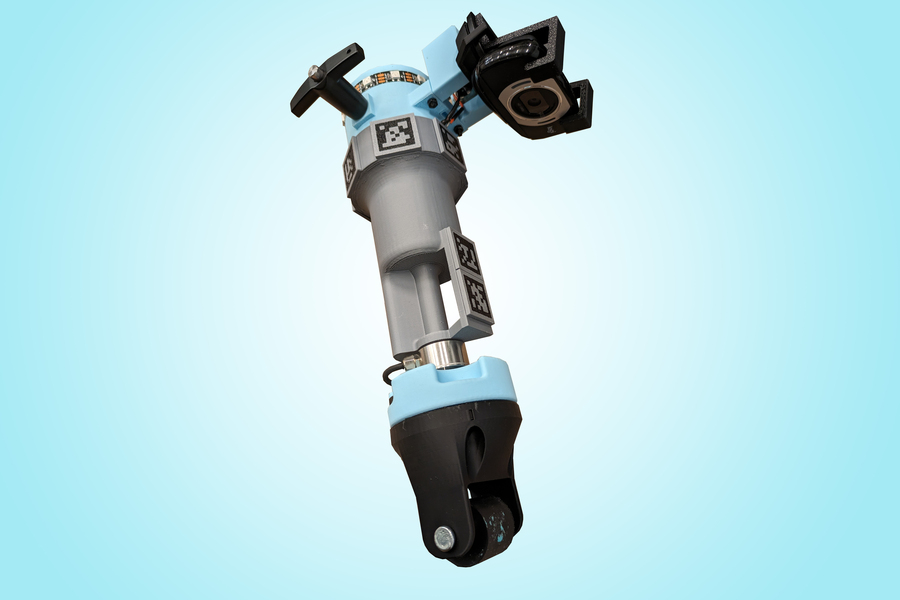
The hand held gadget developed by MIT that can be utilized to show a robotic new expertise. | Credit score: MIT
Coaching collectively
Shah’s group at MIT designs robots that may work alongside people within the office, in hospitals, and at residence. A foremost focus of her analysis is creating techniques that allow individuals to show robots new duties or expertise “on the job,” because it have been. Such techniques would, for example, assist a manufacturing unit ground employee rapidly and naturally regulate a robotic’s maneuvers to enhance its activity within the second, relatively than pausing to reprogram the robotic’s software program from scratch — a ability {that a} employee could not essentially have.
The group’s new work builds on an rising technique in robotic studying known as “studying from demonstration,” or LfD, wherein robots are designed to be skilled in additional pure, intuitive methods. In trying by the LfD literature, Hagenow and Shah discovered LfD coaching strategies developed up to now fall usually into the three foremost classes of teleoperation, kinesthetic coaching, and pure instructing.
One coaching methodology may fit higher than the opposite two for a selected individual or activity. Shah and Hagenow puzzled whether or not they might design a device that mixes all three strategies to allow a robotic to be taught extra duties from extra individuals.
“If we might deliver collectively these three other ways somebody may need to work together with a robotic, it might deliver advantages for various duties and completely different individuals,” Hagenow stated.
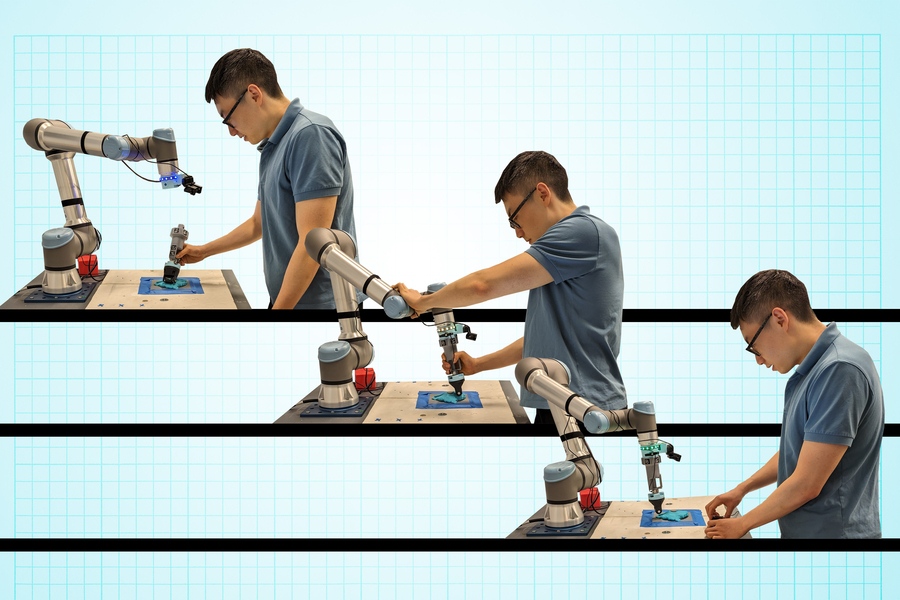
MIT developed a handheld interface that allows you to train a robotic new expertise, utilizing any of three coaching approaches: pure instructing (prime left), kinesthetic coaching (center), and teleoperation. | Credit score: MIT
Duties at hand
With that aim in thoughts, the group engineered a brand new versatile demonstration interface (VDI). The interface is a handheld attachment that may match onto the arm of a typical collaborative robotic arm. The attachment is provided with a digicam and markers that observe the device’s place and actions over time, together with power sensors to measure the quantity of strain utilized throughout a given activity.
When the interface is hooked up to a robotic, your complete robotic could be managed remotely, and the interface’s digicam data the robotic’s actions, which the robotic can use as coaching knowledge to be taught the duty by itself. Equally, an individual can bodily transfer the robotic by a activity, with the interface hooked up. The VDI may also be indifferent and bodily held by an individual to carry out the specified activity. The digicam data the VDI’s motions, which the robotic also can use to imitate the duty when the VBI is reattached.
To check the attachment’s usability, the group introduced the interface, together with a collaborative robotic arm, to a neighborhood innovation heart the place manufacturing consultants study and take a look at expertise that may enhance factory-floor processes. The researchers arrange an experiment the place they requested volunteers on the heart to make use of the robotic and all three of the interface’s coaching strategies to finish two frequent manufacturing duties: press-fitting and molding. In press-fitting, the consumer skilled the robotic to press and match pegs into holes, just like many fastening duties. For molding, a volunteer skilled the robotic to push and roll a rubbery, dough-like substance evenly across the floor of a middle rod, just like some thermomolding duties.
For every of the 2 duties, the volunteers have been requested to make use of every of the three coaching strategies, first teleoperating the robotic utilizing a joystick, then kinesthetically manipulating the robotic, and eventually, detaching the robotic’s attachment and utilizing it to “naturally” carry out the duty because the robotic recorded the attachment’s power and actions.
The researchers discovered the volunteers usually most well-liked the pure methodology over teleoperation and kinesthetic coaching. The customers, who have been all consultants in manufacturing, did provide situations wherein every methodology might need benefits over the others. Teleoperation, for example, could also be preferable in coaching a robotic to deal with hazardous or poisonous substances. Kinesthetic coaching might assist employees regulate the positioning of a robotic that’s tasked with shifting heavy packages. And pure instructing may very well be helpful in demonstrating duties that contain delicate and exact maneuvers.
“We think about utilizing our demonstration interface in versatile manufacturing environments the place one robotic may help throughout a spread of duties that profit from particular kinds of demonstrations,” stated Hagenow, who plans to refine the attachment’s design based mostly on consumer suggestions and can use the brand new design to check robotic studying. “We view this examine as demonstrating how larger flexibility in collaborative robots could be achieved by interfaces that broaden the ways in which end-users work together with robots throughout instructing.”
Editor’s Notice: This text was republished from MIT Information.