Oak Ridge Nationwide Laboratory (ORNL) researchers have created a vacuum-assisted extrusion approach that reduces inside porosity in large-scale 3D-printed polymer components by as much as 75%. The tactic addresses a big limitation in large-format additive manufacturing (LFAM), which has struggled with inside voids that compromise the structural integrity of printed elements. This development may enhance the adoption of LFAM know-how throughout aerospace, automotive, and protection tooling purposes.
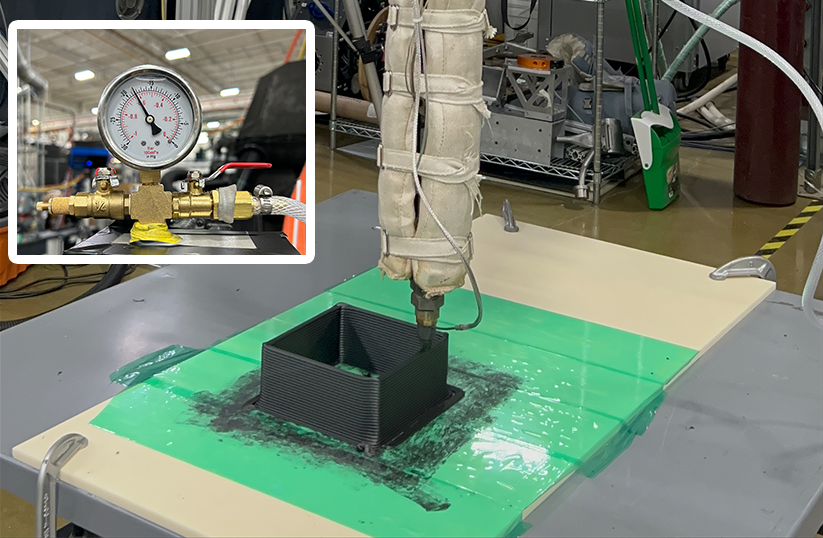
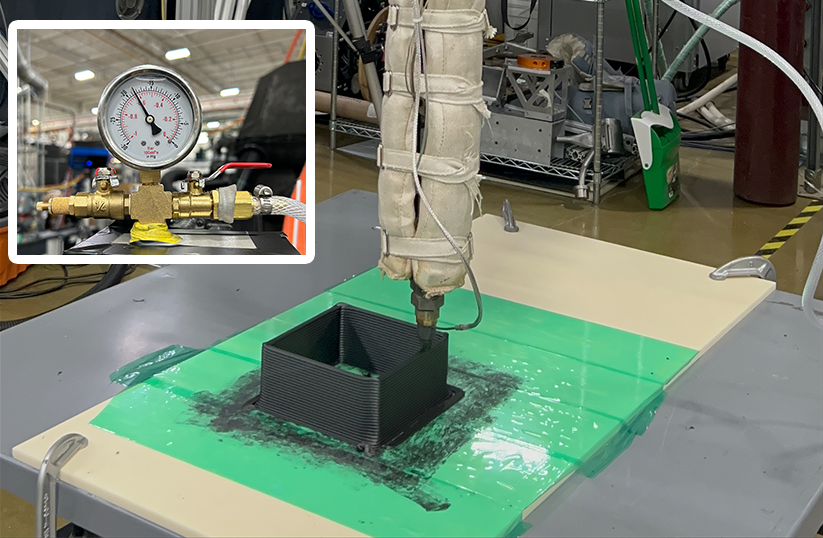
The approach integrates a vacuum hopper through the extrusion course of to take away trapped gases in fiber-reinforced supplies. These supplies, generally utilized in LFAM for his or her stiffness and low thermal growth, usually comprise intrabead porosity that impacts remaining half high quality. Testing confirmed the brand new system lowered porosity to underneath 2%, no matter various fiber content material.
“Utilizing this revolutionary approach, we’re not solely addressing the vital difficulty of porosity in large-scale polymer prints but additionally paving the way in which for stronger composites,” mentioned ORNL’s Vipin Kumar. “This can be a important leap ahead for the LFAM trade.”
The present implementation is designed for batch processing of supplies. Nevertheless, ORNL has already developed a patent-pending idea for steady deposition techniques, which might be explored in future analysis initiatives.
This growth represents significant progress in overcoming one of many key technical challenges going through large-scale 3D printing. By addressing porosity points, the know-how may assist enhance the energy, sturdiness, and efficiency of huge printed elements for industrial purposes.
Supply: ornl.gov