China has accomplished a profitable take a look at flight of its first turbojet engine produced solely by means of 3D printing, based on a press release launched by the Aero Engine Company of China (AECC), a state-owned aerospace propulsion producer. The flight occurred on Tuesday within the Inside Mongolia Autonomous Area and reached an altitude of 4,000 meters (13,000 ft).
AECC acknowledged, “This profitable inaugural flight lays a extra strong technical basis for the analysis and improvement of future superior aviation engines in China.” The engine belongs to the 160-kilogram (353-pound) thrust class and represents the nation’s first turbojet on this class to be validated in flight utilizing additive manufacturing.
The engine was constructed utilizing a mixture of 3D printing and multi-disciplinary topology optimization—a computational strategy that identifies probably the most environment friendly materials distribution inside a component’s geometry. This technique permits the manufacturing of built-in parts with complicated constructions that aren’t possible utilizing typical casting or forging. In response to AECC, this technique allowed engineers to scale back weight whereas sustaining structural integrity.


For China’s aerospace sector, the event addresses a longstanding concern: reliance on international engine suppliers. Producing high-performance turbine parts, equivalent to single-crystal blades, has traditionally required superior supplies and manufacturing methods that China has struggled to totally cultivate. By shifting to additive processes, producers might be able to bypass a number of the technical bottlenecks which have slowed the nation’s progress in jet engine improvement.
Engines on this thrust class are generally utilized in unmanned aerial automobiles (UAVs), notably for high-speed or long-endurance functions. AECC has not disclosed the particular platform used for the take a look at, nor has it launched pictures or information past altitude affirmation. Nevertheless, the burden and measurement recommend relevance for UAV propulsion, slightly than business or crewed techniques.
Shifting from prototype to industrial-scale manufacturing introduces a number of challenges. Growing high-temperature-resistant metallic powders with constant microstructure is important for making certain mechanical efficiency beneath thermal stress. High quality management should be exact, as flaws in vital parts can result in engine failure. Certification procedures for flight security and sturdiness stay time-consuming, notably for solely additively manufactured techniques.
Whereas this take a look at confirms {that a} flight-ready design will be achieved by means of digital manufacturing in China, it stays to be seen whether or not AECC or different home corporations can replicate this outcome throughout a number of models. Standardization and reproducibility might be key benchmarks in figuring out the maturity of this strategy.
Additive manufacturing reshapes rocket engine manufacturing
New Frontier Aerospace (NFA), a U.S.-based propulsion startup, just lately accomplished scorching fireplace testing of its 3D printed Mjölnir rocket engine. Constructed utilizing additive manufacturing and designed with a full-flow staged combustion cycle, Mjölnir is meant for reusable launch automobiles, orbital switch techniques, and hypersonic platforms. The venture has acquired backing from the U.S. Protection Innovation Unit and NASA. Through the use of liquefied pure gasoline, the engine additionally goals to scale back carbon emissions when fueled with bio-waste–derived LNG. NFA plans to combine Mjölnir into upcoming unmanned techniques and provide it as a modular propulsion unit for exterior prospects.
In South Korea, INNOSPACE has established an in-house Superior Manufacturing Division to consolidate 3D printing throughout its rocket engine manufacturing. This vertically built-in unit oversees each step of producing—from design and simulation to machining and high quality management—utilizing proprietary metallic additive applied sciences. In response to the corporate, 3D printing has enabled price reductions of as much as 50%, improved half consistency, and enhanced efficiency by decreasing engine mass. The ability, now licensed beneath ISO/ASTM 52941-20 for aerospace-grade metallic AM, has accomplished fabrication of 13 vital parts for its HANBIT launch automobile and is scaling as much as full manufacturing later this yr.
Prepared to find who received the 2024 3D Printing Business Awards?
Subscribe to the 3D Printing Business e-newsletter to remain up to date with the newest information and insights.
Featured photograph exhibits the 3D printed Turbojet Engine. Picture through AECC.
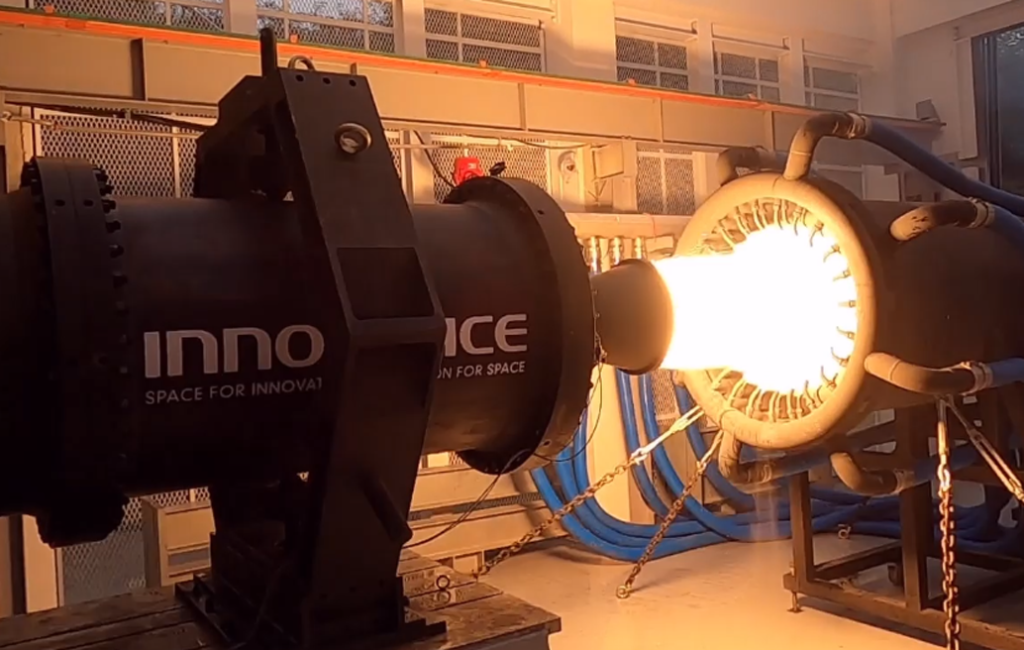
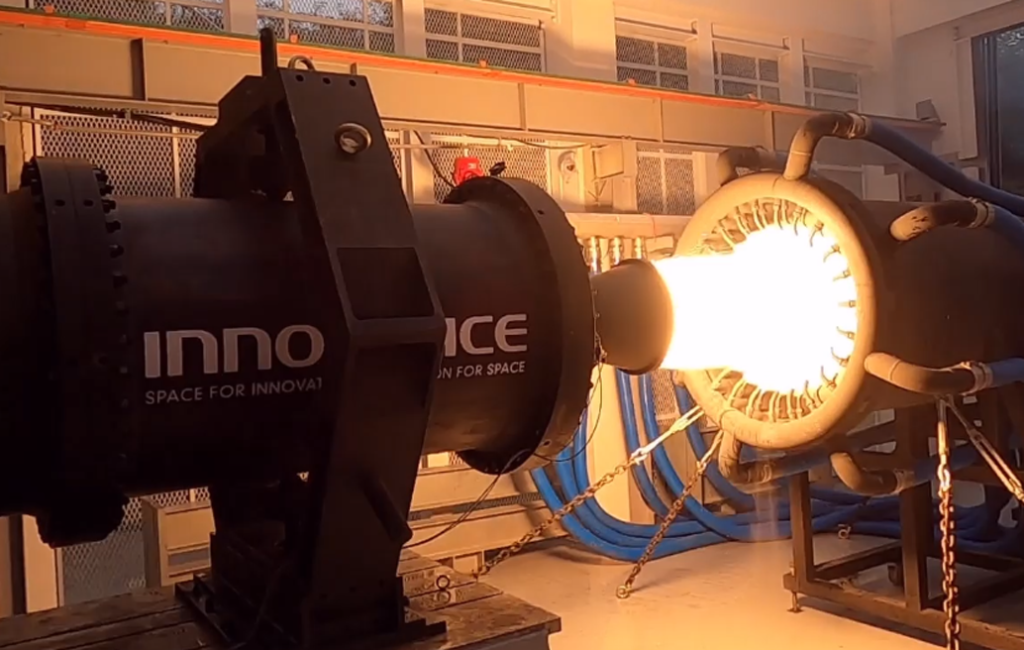