BMW Group has developed a recycling system that converts waste 3D printing powder and used elements into new filament for manufacturing manufacturing instruments and elements. The corporate processes as much as 12 tonnes of waste powder yearly at its Additive Manufacturing Campus in Oberschleißheim, creating recycled filament and granulate to be used throughout its international manufacturing community. The recycled supplies are used to supply auxiliary manufacturing gadgets, instruments, and numerous manufacturing aids by way of Fused Filament Fabrication (FFF) and Fused Granulate Fabrication (FGF) applied sciences.
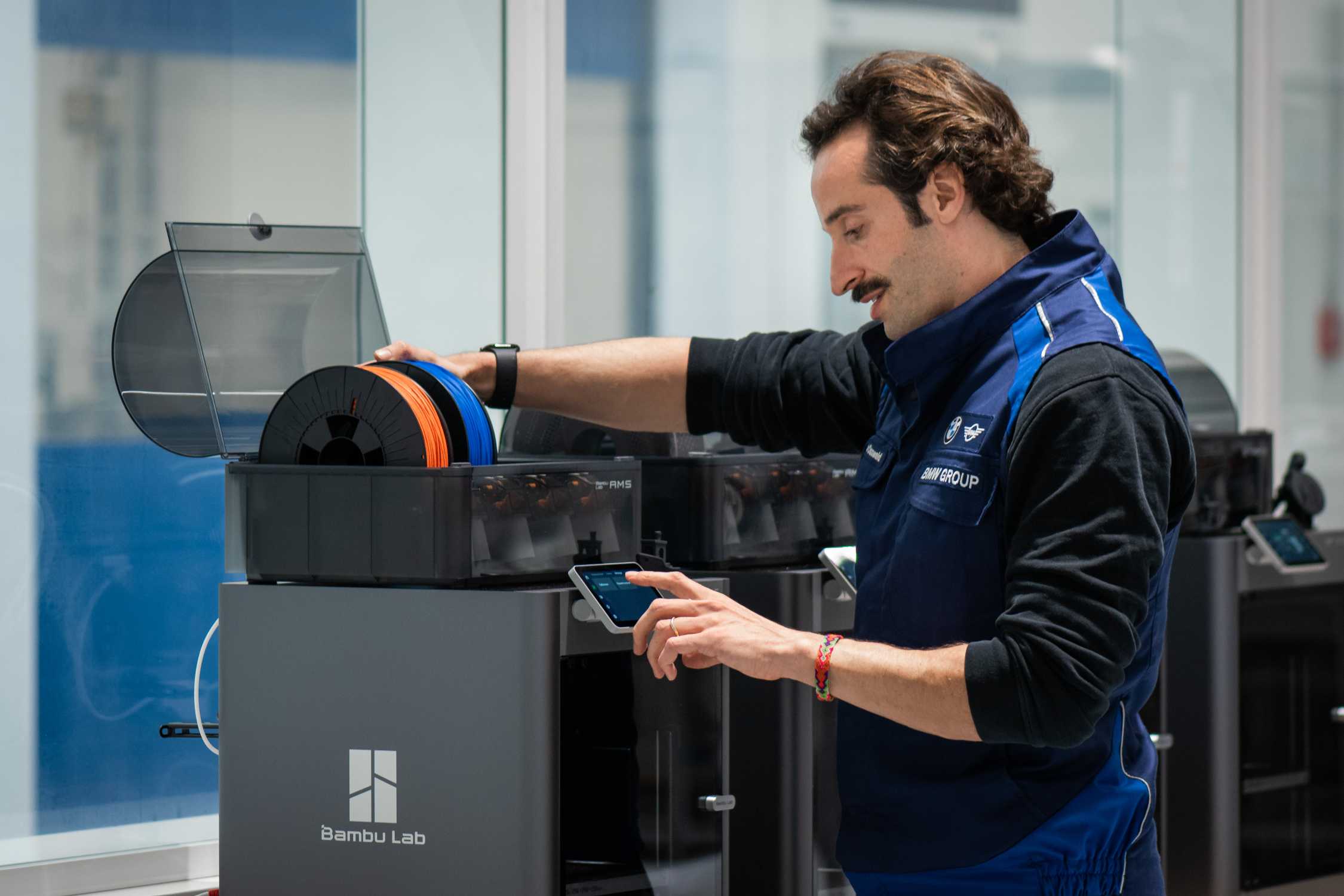
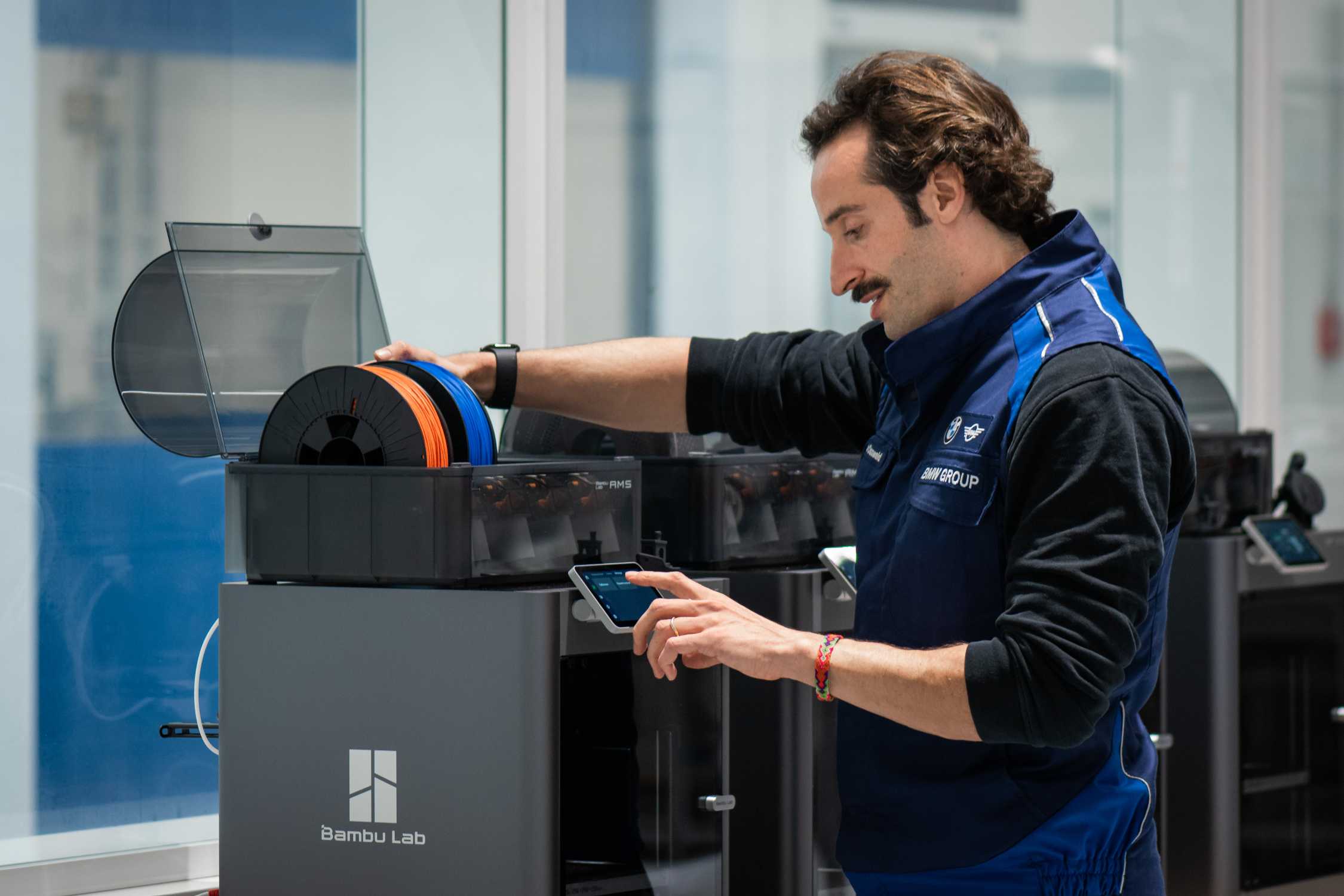
The recycling initiative started in 2018 with the “bottleUP” venture, which initially centered on changing PET bottles into 3D printing materials. By 2019, the corporate began utilizing industrial waste to supply recycled filament on a pilot foundation, and by 2021, BMW efficiently printed its first holders and manufacturing gadgets utilizing recycled supplies. “I’ve been concerned with this venture from the very starting and I’m thrilled to see how far we’ve come – from our preliminary concepts and makes an attempt at startup degree to now with the ability to produce massive portions of extremely sturdy elements from recycled filament at any BMW Group manufacturing location,” says Paul Victor Osswald, venture supervisor for Predevelopment Non-Metals.
BMW’s Additive Manufacturing Campus serves as a middle of competence, offering different manufacturing amenities with recycled filament, optimized printing parameters, and technical experience. The Campus works with established 3D printing amenities at BMW crops to check appropriate printers and develop validated parameter settings for recycled supplies. This complete bundle allows different places to shortly obtain high quality printing outcomes whereas constructing native experience by way of coaching packages.
Each BMW Group plant now operates 3D printers, producing a number of hundred thousand elements yearly for numerous purposes. These embrace ergonomic options for staff, scratch safety, becoming aids, manufacturing gear, gauges, templates, and specialised instruments. Particular examples embrace elements for chassis-body meeting at Plant Munich, help pedestals for motorbike trim ornament in Berlin, and magnetic screw holders developed by staff at Plant Dingolfing to forestall elements loss throughout meeting.
Supply: press.bmwgroup.com