Oak Ridge Nationwide Laboratory’s Manufacturing Demonstration Facility (MDF), in collaboration with reactor developer Kairos Energy and Barnard Development, has developed and deployed large-format 3D printed polymer composite molds to solid high-precision concrete buildings on the Hermes Low-Energy Demonstration Reactor. The varieties, fabricated utilizing carbon-fiber-reinforced ABS, are getting used at Kairos Energy’s Oak Ridge campus in Tennessee. Every part measures roughly 10 by 10 toes and is stacked three items excessive to kind a column.
The printed molds had been used within the Janus shielding demonstration and function a precursor to the formwork that can be applied within the Hermes bioshield system. A portion of 1 column kind was displayed on the East Tennessee Financial Council’s Nuclear Alternatives Workshop, held July 22–23 on the Knoxville Conference Middle. The composite molds allow cast-in-place fabrication of advanced concrete elements in considerably much less time than typical metal or wooden formwork.
“We’re exhibiting that the way forward for nuclear development doesn’t must appear like the previous,” mentioned Ryan Dehoff, director of the MDF. “We’re combining nationwide lab capabilities with MDF’s legacy of taking huge, formidable swings — moonshots that flip daring concepts into sensible options — to speed up new business nuclear power.”
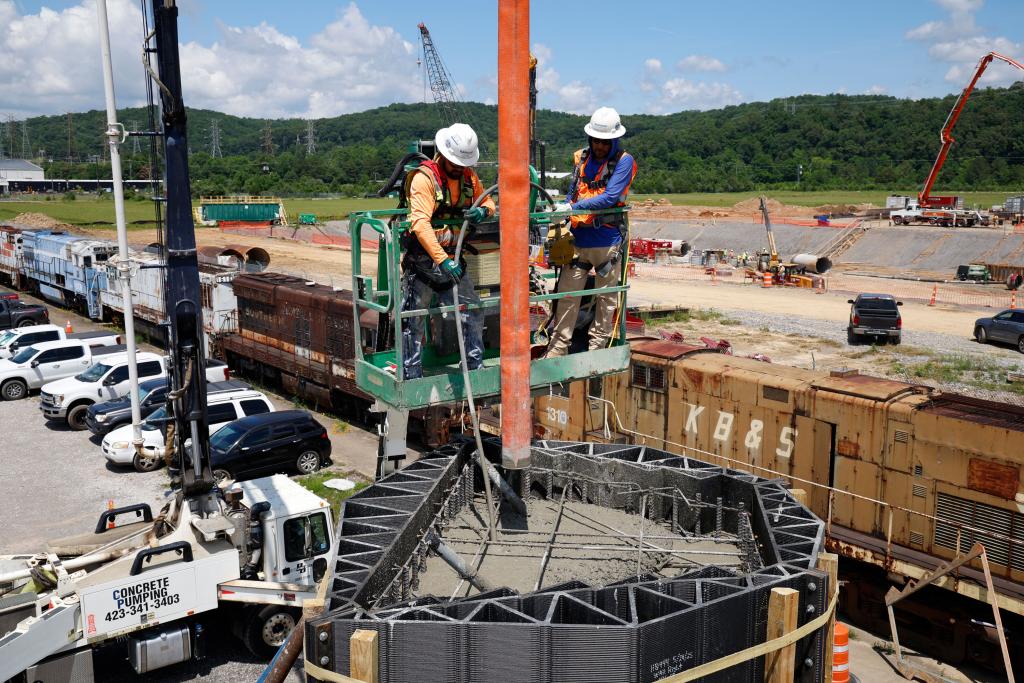
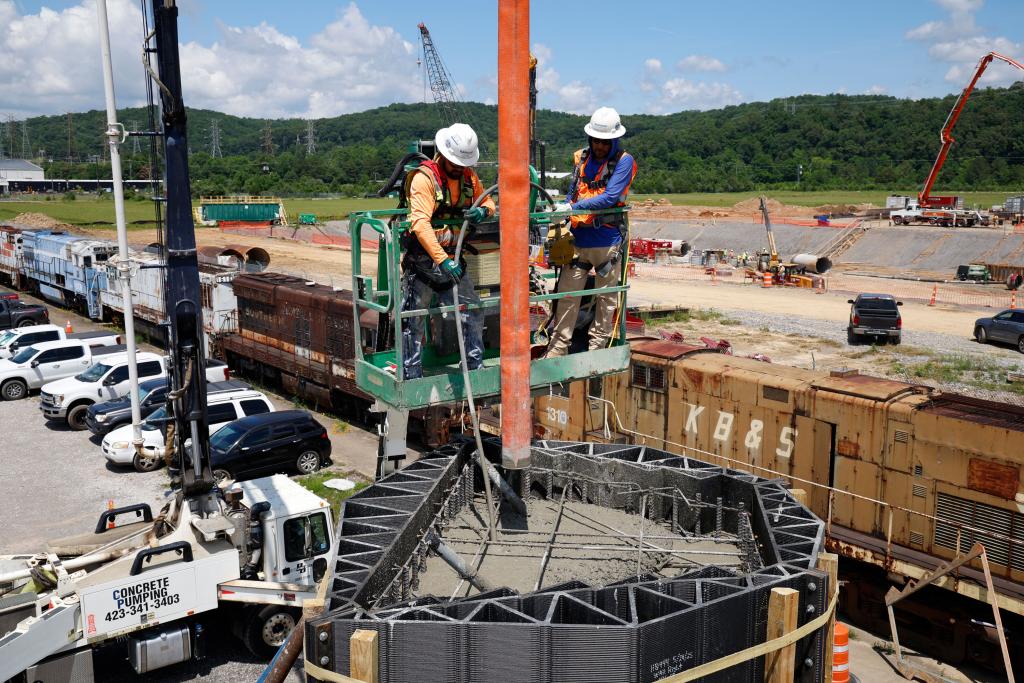
MDF has beforehand led additive manufacturing initiatives throughout sectors, together with the event of 3D printed automobiles and homes and real-time half qualification instruments. The present work applies these ideas to nuclear infrastructure. Kairos Energy’s reactor improvement mannequin emphasizes speedy studying cycles and early-stage validation. Edward Blandford, co-founder and CTO of Kairos Energy, mentioned the collaboration started following recommendation from a business companion: “It’s not typically we get recommendation from trade to name the nationwide lab as a result of they transfer rapidly.”
Blandford defined that the usage of prototype molds allowed the staff to refine methods and cut back threat. “This challenge suits squarely into our iterative improvement strategy,” he mentioned. “By constructing and testing the molds for the columns first, we’re capable of refine our strategies, have interaction early with regulators, and cut back threat earlier than we scale up the development methodology for Hermes and future vegetation.”
The Janus columns display a component of the Hermes bioshield, a thick concrete barrier designed to soak up radiation throughout reactor operation. Based on Ahmed (Arabi) Hassen, composites innovation group chief at ORNL, the molds needed to meet each geometric tolerances and structural necessities to comprise the hydrostatic stress of poured concrete. The printing course of was optimized to make sure mechanical resilience and dimensional stability underneath stress.
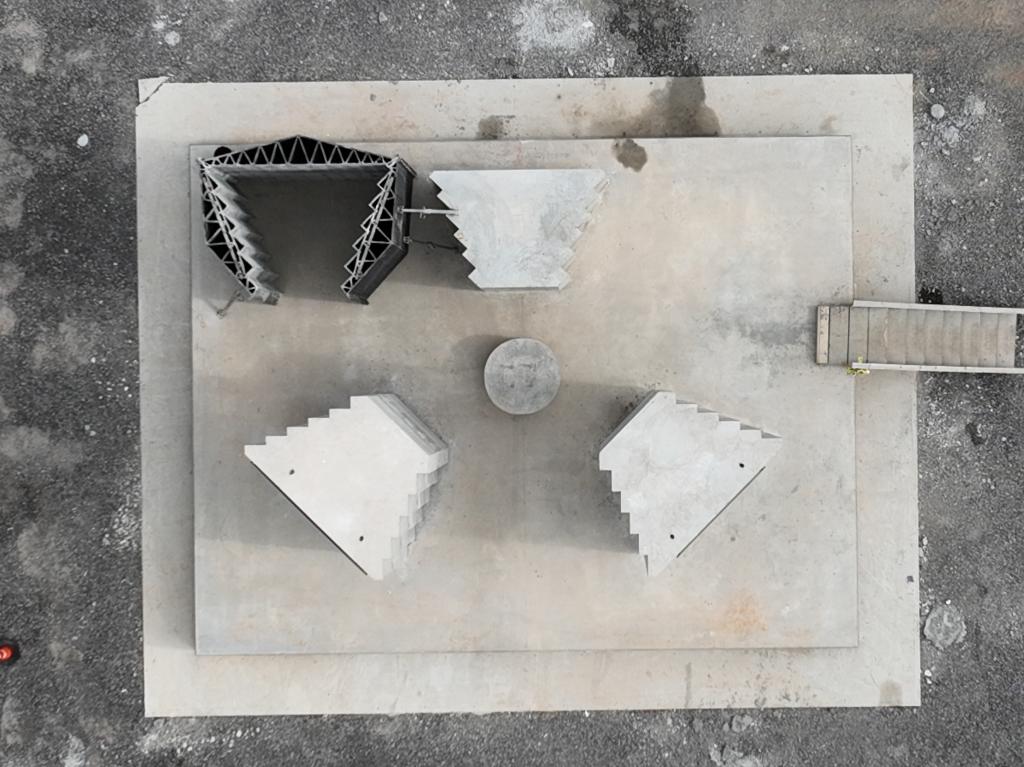
Barnard Development labored straight with MDF and Kairos Energy to implement and adapt the molds within the discipline, offering real-time suggestions and integrating design adjustments to enhance constructability. Trade companions Airtech, TruDesign, Additive Engineering Options, and Haddy supported mould fabrication and logistics, forming a brand new provide chain mannequin for nuclear development by way of additive manufacturing.
The challenge is a part of the SM2ART Moonshot Challenge, a multi-year initiative led by MDF and the College of Maine and funded by the Division of Power’s Superior Supplies and Manufacturing Applied sciences Workplace. This system focuses on modernizing power infrastructure by way of large-scale additive manufacturing, bio-based composite supplies, and built-in digital platforms. ORNL contributes experience in supplies science, supercomputing, and synthetic intelligence, whereas the College of Maine helps structural system improvement and digital manufacturing.
Over the following 18 months, this system will broaden to full-scale manufacturing of formwork for added parts of the Hermes reactor, together with radiation shielding and constructing enclosures. The staff plans to combine digital twins and data-driven high quality assurance whereas transitioning to printable biocomposite feedstocks derived from timber residuals. The fabric technique targets a 75% discount in value utilizing domestically sourced forest byproducts.
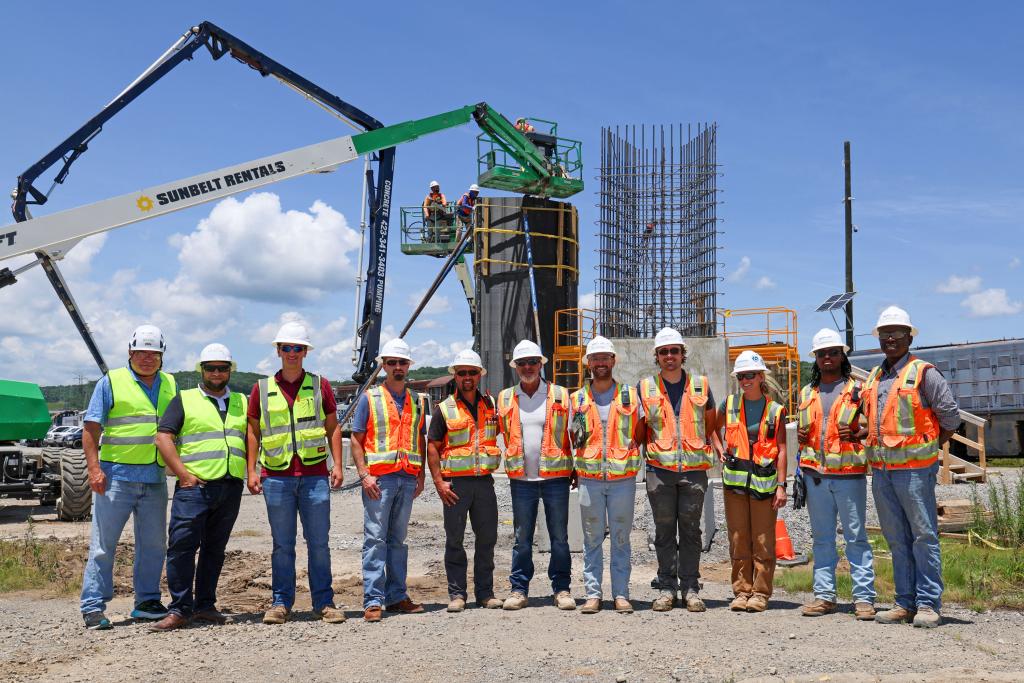
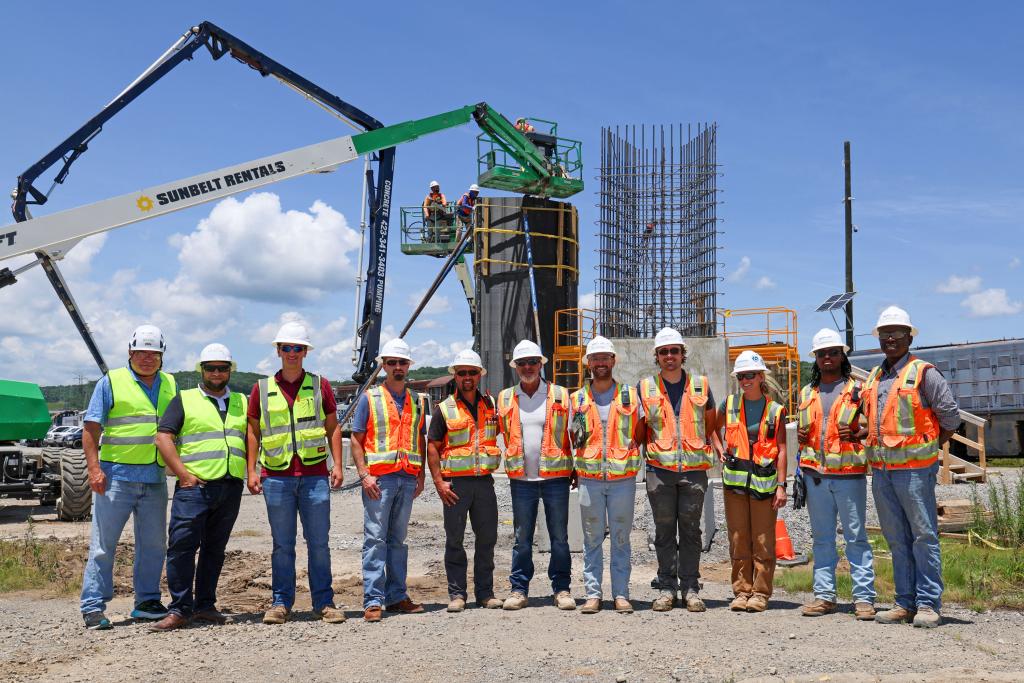
Hermes is the primary superior reactor to obtain a development allow from the U.S. Nuclear Regulatory Fee. Situated inside the Knoxville–Oak Ridge area, the nation’s most concentrated nuclear know-how hall, the reactor represents a case examine in making use of superior manufacturing to fission infrastructure.
“This challenge exhibits that we are able to break by way of previous strategies with new applied sciences that decrease limitations, cut back threat, and speed up development timelines,” mentioned Hassen. “We’re taking the very best of additive manufacturing — modularity, flexibility, speedy iteration — and making use of it to nuclear power.”
UT-Battelle manages Oak Ridge Nationwide Laboratory for the Division of Power’s Workplace of Science, which is the biggest supporter of primary analysis within the bodily sciences in the USA.
Prepared to find who received the 2024 3D Printing Trade Awards?
Subscribe to the 3D Printing Trade e-newsletter to remain up to date with the most recent information and insights.
Featured photograph exhibits trying down on the Janus gate from above, the 3D printed kind is seen subsequent to the concrete pillars organized in a radiation image. Picture through Kairos Energy.