Simulation is rising as an important software for controlling the advanced physics of metallic additive manufacturing, as engineers search to enhance course of reliability and cut back defects. Talking through the 2025 AMUG Convention, Garrett Clyma, a computational fluid dynamics (CFD) engineer at Stream Science, Inc, outlined how soften pool modeling is offering new capabilities to optimize laser processes with out the prohibitive prices of bodily experimentation.
On the coronary heart of the problem lies the extremely localized heating and speedy cooling of metals throughout AM. Instabilities within the soften pool brought on by overheating or underheating lead to defects corresponding to porosity, incomplete fusion, and floor irregularities. “Controlling the fabric habits in AM may be very difficult due to the complexity of all these totally different interactions of the person physics,” Clyma defined.
FLOW-3D AM, is a multi-physics CFD platform designed to seize these phenomena with excessive constancy, enabling engineers to visualise the evolution of soften pool instabilities and preempt defects earlier than committing to pricey construct experiments.
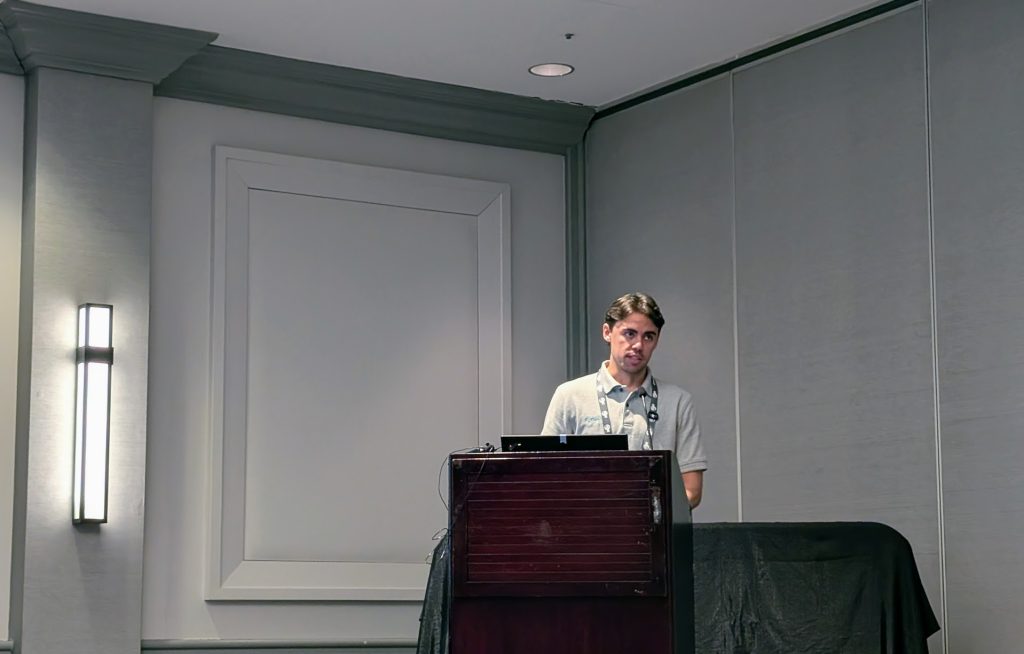
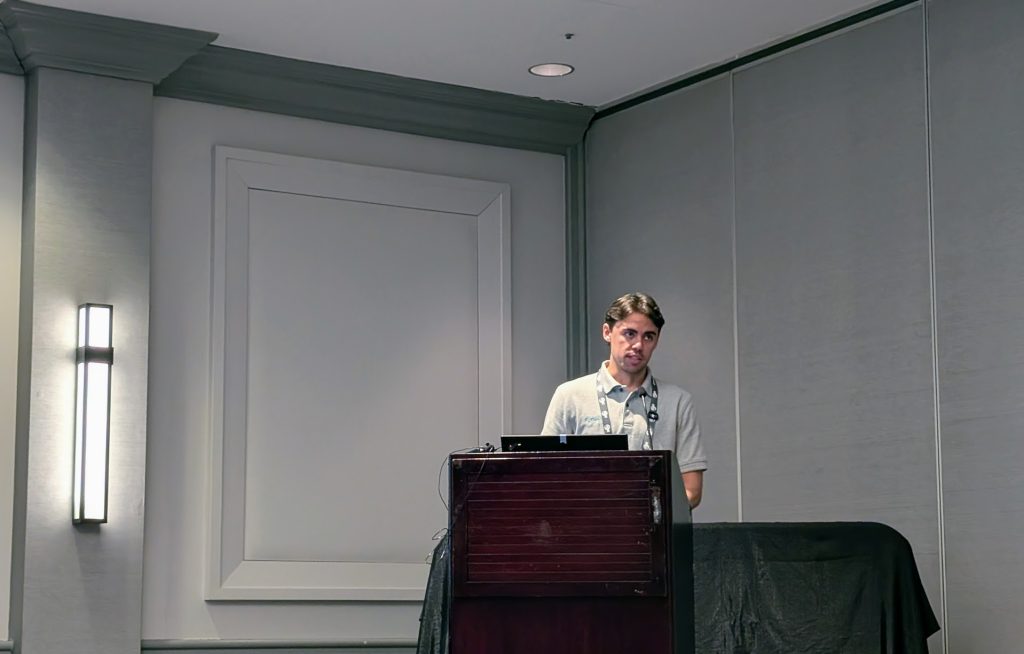
Beam Shaping: A Device for Course of Stability
Laser beam shaping, a longtime follow in welding, is gaining floor in AM as a technique to tailor the spatial power distribution of the beam. Relatively than counting on the normal Gaussian profile, beam shaping distributes power extra evenly or selectively throughout the beam, influencing soften pool habits and solidification traits.
Clyma offered the findings of a research carried out by Dr. Mohamed Bayat’s group on the Technical College of Denmark, which used FLOW-3D AM to analyze ring beam profiles utilized to single-track titanium alloy builds. Validation in opposition to each cross-sectional cuts and in-situ X-ray monitoring demonstrated sturdy alignment between simulation and experiment, with soften pool dimension errors effectively underneath 10 %.
Because the workforce various the ratio of core-to-ring energy whereas sustaining fixed whole laser power, the simulations revealed clear tendencies. Ring beams produced wider, shallower soften swimming pools, avoiding the deep keyholes attribute of Gaussian beams. “The ring beam creates a considerably smaller, much less deep annular melancholy zone, which leads to a extra secure soften pool,” Clyma stated.
At greater laser powers, nevertheless, instabilities resurfaced. Simulations predicted the formation of elongated molten jets and spatter ejection from the soften pool—behaviors that have been subsequently confirmed by high-speed X-ray imaging.


Increasing to Arbitrary Beam Shapes
Constructing on these outcomes, Stream Science carried out an inner research exploring each static and dynamically formed laser beams, together with advanced profiles corresponding to infinity patterns, spirals, and five-dot arrays. Working on a 10-core desktop machine, particular person simulations usually accomplished in underneath six hours, whereas current parallelization developments have enabled even bigger parametric sweeps.
The five-dots configuration, for instance, concentrated power at discrete factors, producing excessive penetration depths underneath keyhole mode situations however restricted effectiveness in conduction mode. “We’re not effectively heating up the soften pool, however simply heating up these single factors,” Clyma defined, emphasizing that beam choice should align with the meant mode of operation.
Decrease most soften pool velocities and extra uniform temperature distributions noticed in spiral and infinity patterns urged that these shapes might provide higher course of stability than concentrated beams. Throughout all circumstances, metrics corresponding to depth, temperature, soften pool velocity, and processing fee offered a constant framework to guage trade-offs earlier than shifting to bodily trials.
“Simulation is a really useful gizmo for serving to to make these selections,” Clyma stated, noting that the rising levels of freedom in laser management require systematic strategies to determine promising beam methods.


Floor Pressure, Optical Results, and Materials Dependence
AMUG Convention attendees raised detailed questions concerning the extent of physics modeled inside FLOW-3D AM. Clyma confirmed that key elements corresponding to temperature-dependent floor pressure, contact angle, and laser absorptivity are included into simulations. Absorptivity, usually missing in revealed materials datasets, may be adjusted as a tuning parameter when required.
Thermo-physical properties are usually sourced from databases corresponding to JMatPro, permitting simulations to mirror the precise habits of alloys underneath soften situations. Correct modeling of laser reflections and multi-bounce phenomena can be supported.
A participant complimented the sturdy settlement between simulation predictions and experimental observations, notably in soften pool form, spatter formation, and transition between conduction and keyhole modes.
Sensible Commerce-offs: Stability Versus Penetration
The session concluded with a dialogue of how totally different beam profiles have an effect on not solely defect formation but additionally materials properties. Whereas Gaussian beams allow deeper penetration and doubtlessly finer grain buildings attributable to steeper thermal gradients, in addition they introduce greater dangers of spatter and porosity. In distinction, ring beams provide enhanced stability and diminished peak temperatures, however could alter solidification patterns.
“It actually simply is determined by your meant objective,” Clyma stated. “If you happen to’re capable of discover the results in simulation fairly than experimentation, it may be much more advantageous.”
FLOW-3D AM supplies outputs corresponding to temperature gradients and cooling charges, that are major drivers of microstructural evolution. Though the software program doesn’t but predict mechanical properties instantly, these outputs allow customers to deduce probably outcomes corresponding to grain measurement, elongation, and affect resistance.
One other engineer elaborated that finer, extra oriented grains (arising from excessive gradients and speedy cooling) usually correlate with improved mechanical properties. FLOW-3D AM’s cell-level decision, usually at 5 million parts or finer, permits for detailed native evaluation of those solidification dynamics.
As simulation capabilities proceed to develop, AM engineers now have a strong toolkit to optimize laser processing methods, cut back defects, and improve the efficiency of printed metallic elements: all earlier than urgent “print” on a machine.
What 3D Printing Tendencies are shaping the business?
Subscribe to the 3D Printing Business publication to maintain up with the most recent 3D printing information. You may also observe us on LinkedIn, and subscribe to the 3D Printing Business YouTube channel to entry extra unique content material.
Featured picture exhibits a visualization of Laser Powder Mattress Fusion Simulation. Picture through Stream Science.