Swedish nuclear energy vegetation are implementing 3D printing to deal with spare components challenges as reactors prolong their working lives to 80 years. In keeping with Björn Forssgren, metallic supplies specialist at Ringhals nuclear energy plant, the power to regulate manufacturing internally might “contribute to elevated availability for our manufacturing items, which means extra fossil-free electrical energy manufacturing.”
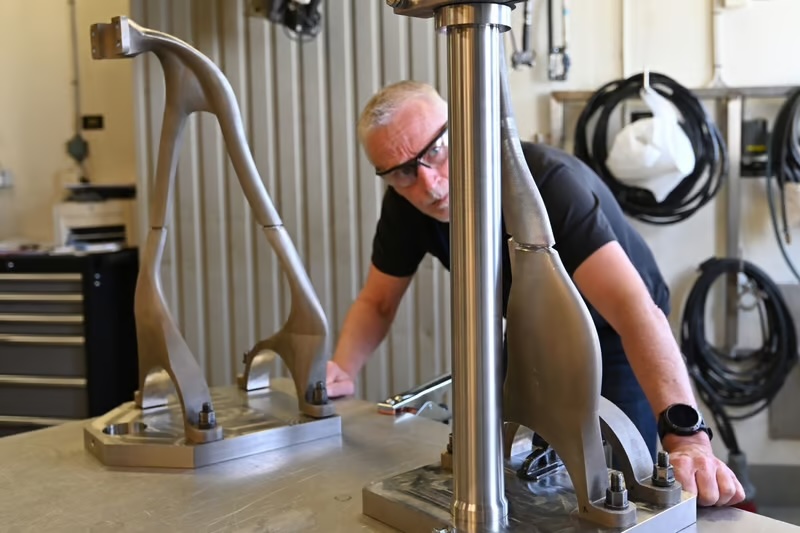
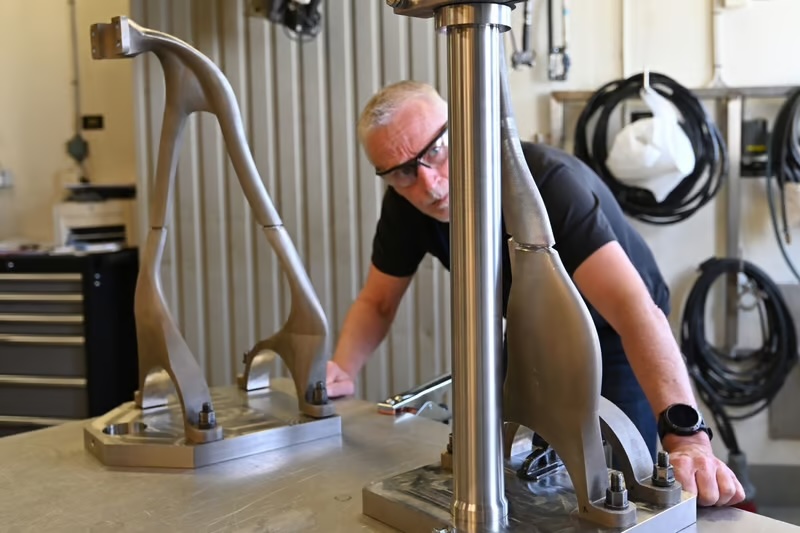
In 2017, Ringhals joined a collaborative 3D printing initiative with different corporations, now managed by Analysis Institutes of Sweden (RISE). The partnership, which has expanded to 21 corporations, focuses on growing AM capabilities for varied elements together with pipes, valves, and pump housings. Testing reveals that 3D-printed components keep equal or superior structural integrity in comparison with historically manufactured elements.
AM-manufactured components are already put in in all three Swedish nuclear energy vegetation: Ringhals, Forsmark, and Oskarshamn. Present functions are restricted to elements not uncovered to excessive strain, although worldwide requirements for pressure-exposed components are in improvement. “We hope that such a typical will likely be prepared within the close to future. As soon as it’s prepared, we will actually begin taking a look at putting in elements in our vegetation,” says Forssgren.
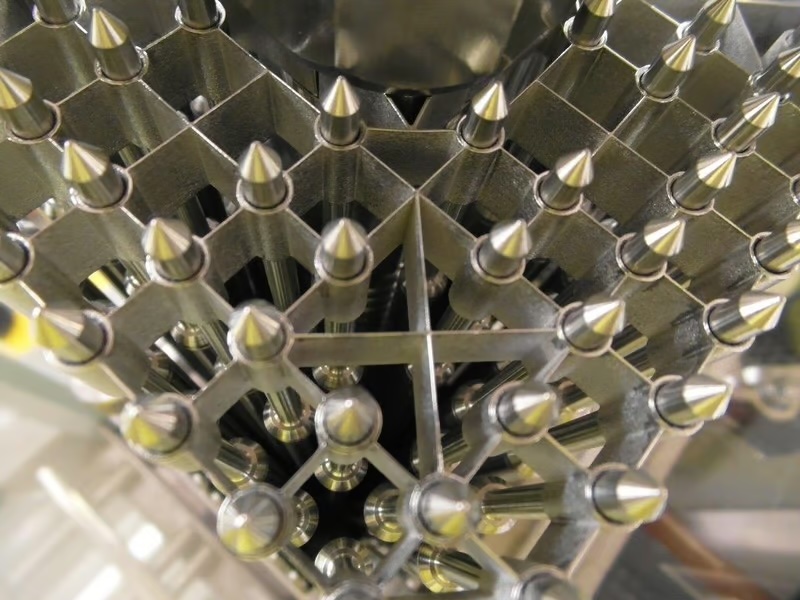
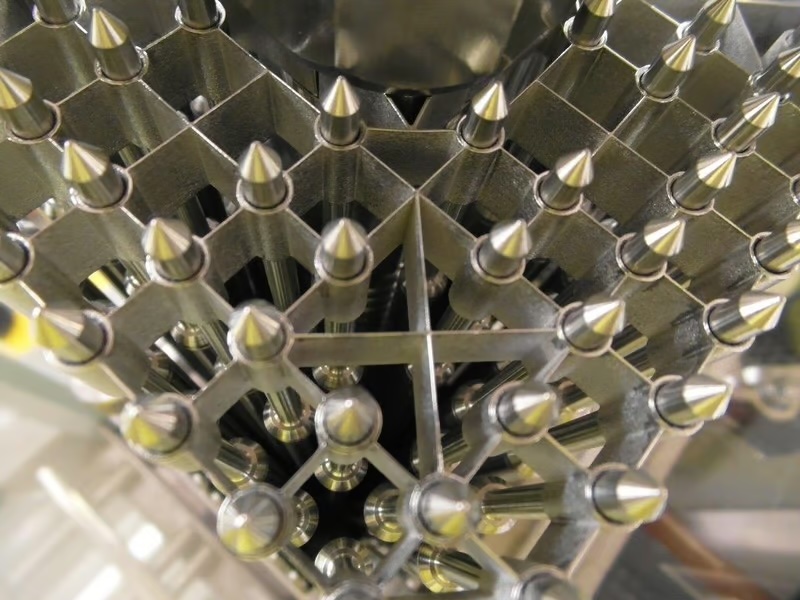
The know-how affords a number of benefits over conventional manufacturing strategies. These embody minimal materials waste, sooner manufacturing instances, and the power to digitally retailer designs fairly than bodily stock. A contemporary 3D printer with 4 laser sources can produce as much as 170 cubic centimeters of fabric hourly, making it an environment friendly manufacturing technique.
Vattenfall, which owns 5 of Sweden’s six nuclear reactors, is exploring the opportunity of establishing an in-house 3D printing facility. Such a facility might doubtlessly provide components to different nuclear vegetation and energy era services inside the firm. “The vegetation usually are not getting any youthful, and AM is a device for reaching our availability targets and decreasing the chance of manufacturing disruptions,” Forssgren explains.
Supply: group.vattenfall.com