Chicago-based 3D printing high quality assurance software program developer Phase3D has launched a brand new inspection system designed to enhance high quality assurance (QA) in chilly spray additive manufacturing (CSAM).
Supported by $1.25 million in funding from the Air Drive Analysis Laboratory (AFRL), the system, referred to as Fringe Inspection: Chilly Spray, makes use of structured mild to seize floor information in actual time in the course of the spray course of. It was examined on the College of Dayton Analysis Institute (UDRI) and later validated in an operational surroundings at Ellsworth Air Drive Base.
CSAM has lengthy offered challenges in sustaining constant high quality as a result of nature of the fabric deposition course of. Phase3D’s system addresses these challenges by offering real-time information that enable for rapid identification of surface-level defects comparable to cracking, cratering, and pitting.
The system additionally evaluates the flatness and total form of the deposited floor, providing technicians the chance to regulate course of parameters dynamically, thereby decreasing materials waste and enhancing effectivity.
“The profitable completion of this challenge underscores the significance of real-time inspection in additive manufacturing, ”stated Niall O’Dowd, Founder and CEO of Phase3D. “The deployment at Ellsworth AFB proves that structured mild inspection is a game-changer for chilly spray purposes. This know-how not solely ensures higher-quality repairs but additionally delivers important price and time financial savings for the Air Drive.”
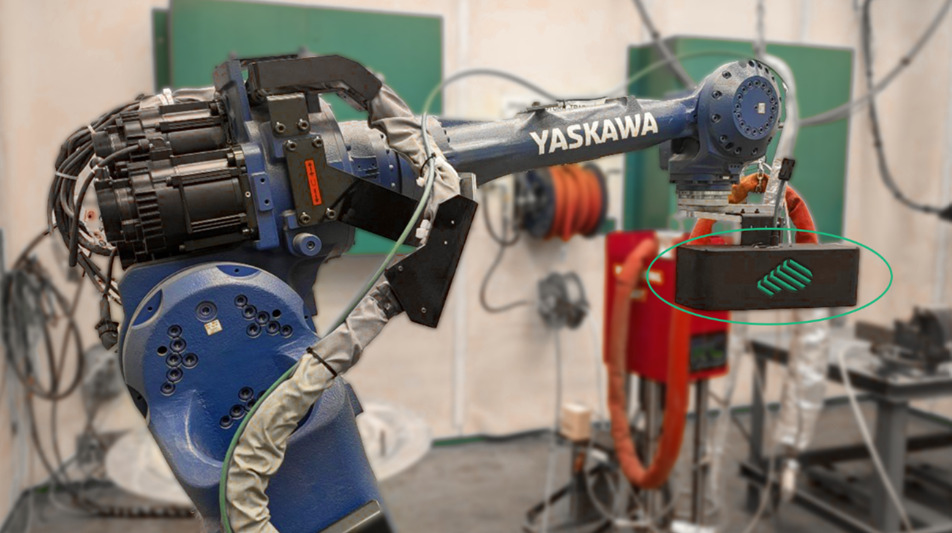
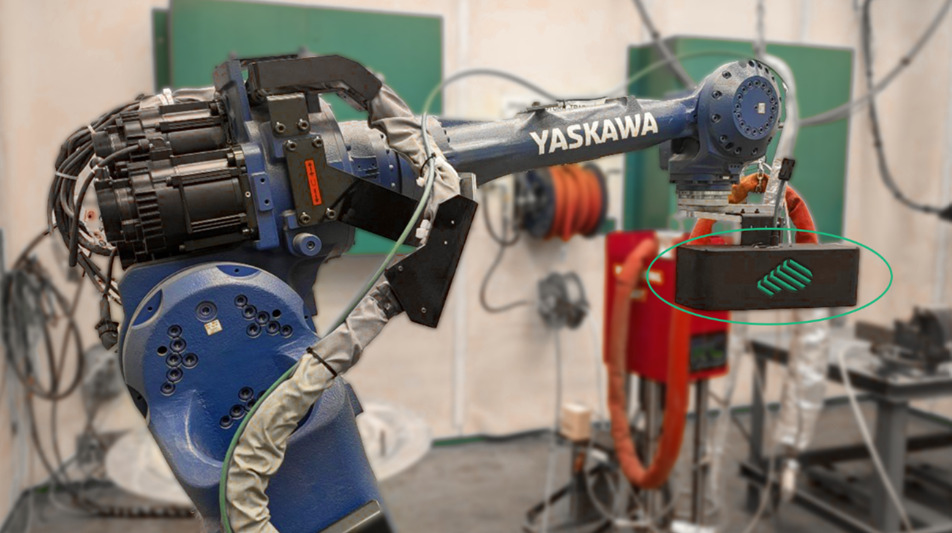
Validated by real-world testing
The Fringe Inspection : Chilly Spray {hardware} is mounted to a robotic arm, the place it collects thousands and thousands of measurement factors associated to layer thickness, roughness, and form. Phase3D developed and deployed each the {hardware} and its accompanying software program suite, Fringe Operator, which is used to interpret inspection information and doc part-specific high quality metrics.
Working with Air Drive engineers, the group established data-driven benchmarks for acceptable and unacceptable deposition high quality, drawing on chilly spray samples created with helium and nitrogen as provider gases. These examples knowledgeable the creation of a go/no-go threshold system to guage elements in the course of the manufacturing course of.
To validate this strategy, Phase3D carried out a blind take a look at utilizing the standard thresholds it had developed. Parts had been evaluated utilizing real-time information collected in the course of the construct course of, and defects comparable to uneven spray patterns and floor discontinuities had been recognized and categorized.
The profitable classification of take a look at specimens additional confirmed the utility of the system for in-situ inspection in chilly spray environments. This challenge was carried out beneath the STTR Part II Proposal F2-16465 – In-Situ Monitoring for Blown Powder Additive Manufacturing contract.
A separate case research involving a laser powder mattress fusion (LPBF) part 3D printed on an EOS M270 machine additional demonstrated the sensible advantages of Fringe Inspection know-how.
An undisclosed aerospace producer confronted half failures attributable to inconsistent porosity and inner geometries, traced to powder buildup on the recoater blade that intermittently dropped onto the construct floor, a problem technicians suspected however couldn’t affirm utilizing normal imaging instruments.
After putting in Fringe Inspection on the machine, the difficulty turned instantly seen by high-resolution heightmaps. The system detected powder drops of as much as 200 µm, 4 instances the traditional layer thickness, falling onto the soften pool.
The invention led to a easy repair: including a set blade on the recoater’s residence place to forestall powder buildup. After implementation, powder-related construct failures stopped completely, decreasing annual losses of $63,000 by over 90%, not together with oblique engineering and troubleshooting prices.
Following these profitable implementations, Phase3D plans to develop the appliance of its structured mild inspection programs past chilly spray. The corporate is at the moment participating with the U.S. Division of Protection (DoD) and private-sector companions to discover extra use instances and help broader adoption of real-time high quality monitoring in additive manufacturing.
The case research relies on reported findings and represents an actual set of occasions. No confidential figures had been used, and all information has been recreated to guard buyer privateness.


High quality assurance in 3D printing
In-situ high quality assurance is important for industries like aerospace and area, the place requirements are excessive, prompting many AM firms to develop their very own novel options.
For instance, Siemens Vitality and threat administration agency DNV partnered to develop a brand new industrial high quality assurance platform by integrating Siemens’ AM Cockpit with DNV’s Unbiased High quality Monitor (IQM). The platform allows real-time monitoring, digital validation, and comparability of 3D printed elements towards authorised fashions.
It supplies automated certification and goals to help zero-defect manufacturing, notably in powder mattress fusion processes. Developed beneath the EU-funded InterQ challenge, the mixed system is designed to strengthen confidence in AM for essential sectors like power, with Siemens highlighting its function in enabling fuel generators to function on low-carbon fuels comparable to hydrogen.
Through the Formnext 2022, MakerVerse and ZEISS launched enhanced high quality assurance instruments on the MakerVerse platform by the mixing of ZEISS’s specialised metrology options. These additions included Tactile CMM, Optical 3D Scanning, Industrial CT and X-Ray capabilities, together with floor roughness measurement. MakerVerse CEO Dr. Markus Seibold emphasised that this alliance “is the proper answer for our prospects needing industrial-grade high quality inspections and reviews for his or her AM elements.”
What 3D printing traits must you be careful for in 2025?
How is the way forward for 3D printing shaping up?
To remain updated with the most recent 3D printing information, don’t neglect to subscribe to the 3D Printing Trade e-newsletter or comply with us on Twitter, or like our web page on Fb.
When you’re right here, why not subscribe to our Youtube channel? That includes dialogue, debriefs, video shorts, and webinar replays.
Featured picture reveals Fringe Inspection : Chilly Spray attaches to the robotic management arm and scans chilly spray deposits in the course of the printing course of. Photograph through Phase3D.